Method for integrally utilizing high-iron-content bauxite
A high-speed iron bauxite and immersion iron technology, applied in chemical instruments and methods, iron oxides, ammonia compounds, etc., can solve the problems of high energy consumption, short furnace lining life, large electrical energy consumption, etc., and meet the requirements of simple process flow and equipment. The effect of low cost and low production cost
- Summary
- Abstract
- Description
- Claims
- Application Information
AI Technical Summary
Problems solved by technology
Method used
Image
Examples
Embodiment 1
[0029] The main composition of the high-iron and low-grade bauxite used is: Al 2 o 3 29.8%, Fe 2 o 3 50.7%, SiO 2 14.0%, TiO 2 1.8%, MnO 1.5%, other 2.2%.
[0030] Crush the high-iron bauxite, grind it down to 80 μm, and mix it evenly with 70% sulfuric acid at a mass ratio of 1:2.2. The material is roasted at 350°C and kept at a constant temperature for 2 hours. The flue gas generated by the reaction is absorbed by dilute sulfuric acid, and then returned to Roasting.
[0031] Add water to dissolve the roasted clinker, the mass ratio of water and clinker is 3:1, dissolve at 50°C for 60 minutes, filter to obtain a mixed solution of aluminum slag, iron sulfate, and aluminum sulfate, and use the aluminum slag directly as micro-silicon powder.
[0032] Use saturated ammonium carbonate solution to adjust the pH of the clinker solution to 1.5, add jarosite seeds, stir and react at 80°C for 2 hours, then filter, the filtrate mainly contains NH 4 + 、Al 3+ , SO 4 2- and a...
Embodiment 2
[0038] The main composition of the high-iron and low-grade bauxite used is: Al 2 o 3 27.9%, Fe 2 o 3 49.2%, SiO 2 15.7%, TiO 2 1.7%, MnO 1.6%, other 3.9%.
[0039] Crush the high-iron bauxite, grind it down to 80 μm, and mix it with 98% concentrated sulfuric acid at a mass ratio of 1:2.5. The material is roasted at 500°C and kept at a constant temperature for 1 hour. The flue gas generated by the reaction is absorbed by dilute sulfuric acid, and then returned to use for roasting.
[0040] Add water to dissolve the roasted clinker, the mass ratio of water to clinker is 5:1, dissolve at 90°C for 30 minutes, filter to obtain a mixed solution of aluminum slag, iron sulfate, and aluminum sulfate, and use the aluminum slag directly as micro-silicon powder.
[0041] Use saturated ammonium carbonate solution to adjust the pH of the clinker solution to 2.0, add jarosite seeds, stir and react at 90°C for 1 hour, filter, and the filtrate contains NH 4 + 、Al 3+ , SO 4 2- an...
PUM
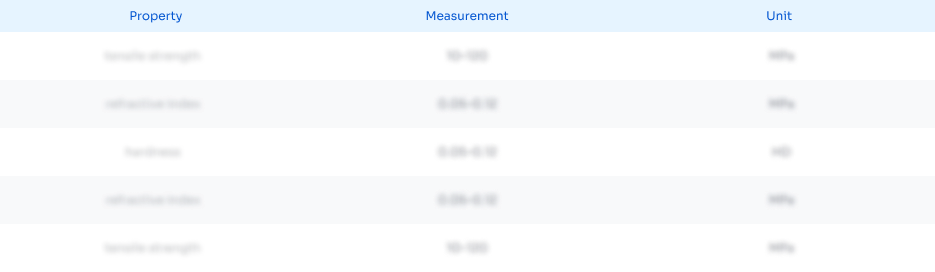
Abstract
Description
Claims
Application Information

- Generate Ideas
- Intellectual Property
- Life Sciences
- Materials
- Tech Scout
- Unparalleled Data Quality
- Higher Quality Content
- 60% Fewer Hallucinations
Browse by: Latest US Patents, China's latest patents, Technical Efficacy Thesaurus, Application Domain, Technology Topic, Popular Technical Reports.
© 2025 PatSnap. All rights reserved.Legal|Privacy policy|Modern Slavery Act Transparency Statement|Sitemap|About US| Contact US: help@patsnap.com