Dynamic kinetic resolution method of 1-(1-naphthyl) ethylamine
A technology of dynamic kinetics and ethylamine, applied in the field of dynamic kinetics splitting of 1-ethylamine, can solve the problems of expensive resolving agent, many product side reactions, slow reaction rate, etc. The effect of high purity, fast reaction rate and great application value
- Summary
- Abstract
- Description
- Claims
- Application Information
AI Technical Summary
Problems solved by technology
Method used
Image
Examples
Embodiment 1
[0022] 1) Add p-chlorophenol, propionic acid, dicyclohexylcarbodiimide and 4-dimethylaminopyridine with a molar ratio of 1:1:1:0.03, stir and react for 7 hours, filter, dry the filtrate, concentrate, pass column, obtain p-chlorophenyl propionate as an acyl donor for subsequent use;
[0023] 2) Add palladium chloride and barium sulfate with a mass ratio of 1:6, heat in 80mL water at 80°C for 1h, add formaldehyde with a mass percentage concentration of 37% and a mass percentage concentration of 30% sodium hydroxide with a volume ratio of 1:1, 80 Heated at ℃ for 30 min, centrifuged, washed with water, dried overnight under low vacuum at 60 ℃, and the obtained solid was used as a racemic catalyst for later use;
[0024] 3) Add racemic 1-(1-naphthyl)ethylamine and p-chlorophenyl propionate, 20 mg / mL lipase and 40 mg racemic catalyst at a molar ratio of 1:1.05 in 3 mL of toluene and place in 30 mL stainless steel The reactor was hydrogenated, and the hydrogen pressure was 0.01MPa t...
Embodiment 2
[0026] 1) Add p-chlorophenol, n-butyric acid, dicyclohexylcarbodiimide and 4-dimethylaminopyridine in a molar ratio of 1:2:2:0.05, stir for 3 hours, filter, dry the filtrate, concentrate, Go through the column to obtain p-chlorophenyl n-butyrate as an acyl donor for subsequent use;
[0027] 2) Add palladium chloride and barium sulfate with a mass ratio of 1:6, heat in 80mL water at 80°C for 1h, add formaldehyde with a mass fraction of 37% and sodium hydroxide with a mass fraction of 30% at a volume ratio of 1:1, Heat at 100°C for 30 min, centrifuge, wash with water, and dry overnight under low vacuum at 60°C, and the obtained solid is used as a racemic catalyst for later use;
[0028] 3) In 3 mL of toluene, add 1-(1-naphthyl) ethylamine and p-chlorophenyl n-butyrate with a molar ratio of 1:1.3, 20 mg / mL lipase and 40 mg rac catalyst in 30 mL stainless steel The reactor was hydrogenated, and the hydrogen pressure was 0.1MPa to react for 15 hours, and the reaction temperature w...
Embodiment 3
[0030] 1) Add p-chlorophenol, n-valeric acid, dicyclohexylcarbodiimide and 4-dimethylaminopyridine with a molar ratio of 1:1.5:1.5:0.05, stir and react for 6 hours, filter, dry the filtrate, concentrate, Go through the column to obtain p-chlorophenyl valerate as an acyl donor for subsequent use;
[0031] 2) Add palladium chloride and barium sulfate with a mass ratio of 1:6, heat in 80mL water at 80°C for 1h, add formaldehyde with a mass fraction of 37% and sodium hydroxide with a mass fraction of 30% at a volume ratio of 1:1, Heat at 80°C for 30 min, centrifuge, wash with water, dry overnight under low vacuum at 60°C, and the obtained solid is used as a racemic catalyst for later use;
[0032] 3) In 3 mL of toluene, add racemic 1-(1-naphthyl)ethylamine and p-chlorophenyl pentanoate with a molar ratio of 1:1.05, 20 mg / mL lipase and 40 mg racemic catalyst in 30 mL stainless steel The reactor was hydrogenated, and the hydrogen pressure was 0.1MPa to react for 15 hours, and the r...
PUM
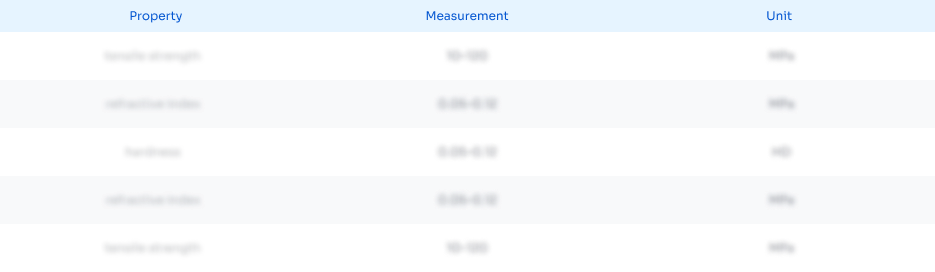
Abstract
Description
Claims
Application Information

- R&D
- Intellectual Property
- Life Sciences
- Materials
- Tech Scout
- Unparalleled Data Quality
- Higher Quality Content
- 60% Fewer Hallucinations
Browse by: Latest US Patents, China's latest patents, Technical Efficacy Thesaurus, Application Domain, Technology Topic, Popular Technical Reports.
© 2025 PatSnap. All rights reserved.Legal|Privacy policy|Modern Slavery Act Transparency Statement|Sitemap|About US| Contact US: help@patsnap.com