Low-temperature self-crosslinking polyacrylate pigment printing binding agent and preparation method thereof
A technology of polyacrylate and pigment printing, applied in the direction of ester copolymer adhesives, adhesive types, etc., can solve the problems of hand feeling, environmental protection, fastness and stability, etc., achieve bright color, low cost, The effect of the simplicity of the polymerization process
- Summary
- Abstract
- Description
- Claims
- Application Information
AI Technical Summary
Problems solved by technology
Method used
Examples
Embodiment 1
[0028] 50.0 g of butyl acrylate, 25.0 g of isooctyl acrylate, 13.0 g of methyl methacrylate, 4.0 g of acrylonitrile, 2.0 g of methacrylic acid, 3.0 g of hydroxypropyl acrylate, 2.0 g of diacetone acrylamide, and 1.7 g of emulsifier g, 60g of deionized water, uniformly stirred to make a pre-emulsion; 0.4g of potassium persulfate was dissolved in 8.0g of deionized water to prepare an initiator solution; in the polymerization reactor, add 25.0g of deionized water and 0.8 g and 0.3 g of sodium bicarbonate, stir evenly; add 14 g of the above-mentioned pre-emulsion and 2 g of the above-mentioned initiator solution to the polymerization reactor, heat up to 78 ° C, and after the blue light appears in the emulsion in the polymerization reactor, pour the Continuously drop the remaining pre-emulsion and initiator solution 6g in the medium, after 2 hours of continuous dripping, add the remaining initiator solution, raise the temperature to 85°C, keep it for 1h, then lower the temperature t...
Embodiment 2
[0032] 60.0 g of butyl acrylate, 16.0 g of isooctyl acrylate, 10.0 g of methyl methacrylate, 4.0 g of acrylonitrile, 2.0 g of methacrylic acid, 4.0 g of hydroxypropyl acrylate, 2.5 g of diacetone acrylamide, and 2.0 g of emulsifier g, 60g of deionized water, uniformly stirred to make a pre-emulsion; 0.35g of potassium persulfate was dissolved in 7.0g of deionized water to prepare an initiator solution; in the polymerization reactor, add 25.0g of deionized water and 1.0 g and 0.2 g of sodium bicarbonate, and stir evenly; add 15 g of the above-mentioned pre-emulsion and 2.5 g of the above-mentioned initiator solution to the polymerization reactor, and heat up to 80° C. Continuously drop the remaining pre-emulsion and initiator solution 7g into the kettle, after 3 hours of continuous dripping, add the remaining initiator solution, raise the temperature to 90°C, keep it warm for 0.5h, then lower the temperature to below 40°C, Adjust the pH value to 7; dissolve 1.5g of adipic acid ...
Embodiment 3
[0036] 68.0g of butyl acrylate, 8.0g of ethyl acrylate, 7.0g of methyl methacrylate, 7.0g of styrene, 2.5g of methacrylic acid, 3.0g of hydroxypropyl acrylate, 3.0g of diacetone acrylamide, 2.0g of emulsifier , 60g of deionized water, stirred evenly to make a pre-emulsion; 0.35g of potassium persulfate was dissolved in 7.0g of deionized water to prepare an initiator solution; in the polymerization reactor, 25.0g of deionized water and 1.0g of emulsifier were added And sodium bicarbonate 0.2g, stir evenly; Add above-mentioned pre-emulsion 16g and above-mentioned initiator solution 2.3g in the polymerization reactor, be warmed up to 82 ℃, after the blue light appears in the emulsion in the polymerization reactor, then add to the polymerization reactor Continuously drop the remaining pre-emulsion and initiator solution 8g in the medium, after 2.5 hours of continuous dropping, add the remaining initiator solution, raise the temperature to 88°C, keep it for 1h, then lower the temper...
PUM
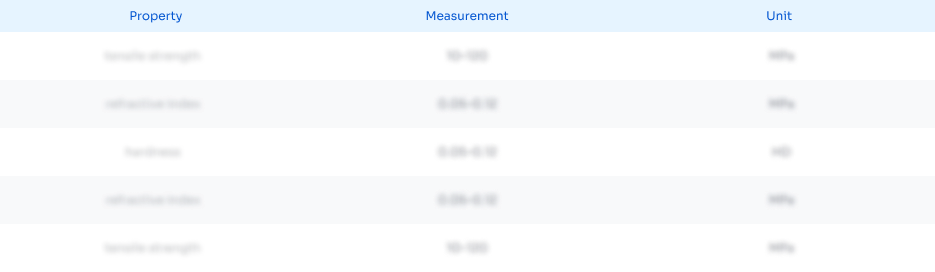
Abstract
Description
Claims
Application Information

- R&D
- Intellectual Property
- Life Sciences
- Materials
- Tech Scout
- Unparalleled Data Quality
- Higher Quality Content
- 60% Fewer Hallucinations
Browse by: Latest US Patents, China's latest patents, Technical Efficacy Thesaurus, Application Domain, Technology Topic, Popular Technical Reports.
© 2025 PatSnap. All rights reserved.Legal|Privacy policy|Modern Slavery Act Transparency Statement|Sitemap|About US| Contact US: help@patsnap.com