Preparation of hydrogenated pyromellitic acid ester
A technology for hydrogenating pyromellitic acid esters and pyromellitic acid, which is applied in the preparation of organic compounds, carboxylate esters, organic chemistry, etc., can solve the problems of rapid catalyst deactivation, frequent regeneration, and short service life. Achieve the effects of improving anti-sintering ability, improving dispersion and high selectivity
- Summary
- Abstract
- Description
- Claims
- Application Information
AI Technical Summary
Problems solved by technology
Method used
Image
Examples
Embodiment 1
[0029] Mix commercially available pseudo-boehmite and aluminum hydroxide powder in a certain proportion to form a uniform powder, weigh quantitative dilute nitric acid and phosphoric acid to prepare an aqueous solution, and spray the prepared solution evenly on the powder in a kneader , and then spray quantitative polyethylene glycol aqueous solution evenly in the mixture, after aging for a certain period of time, extrude on a twin-screw extruder, dry and roast under preset program temperature control to obtain strip-shaped composite alumina , crushed and sieved to take a certain particle size carrier to obtain the composite catalyst carrier used in the present invention. Prepare the following 1-7 carriers according to different raw material ratios:
[0030] Table 1 Preparation and characterization of composite alumina carrier
[0031]
Embodiment 2
[0033] Weigh 100g of carriers 1 to 7 in Example 1, respectively put them into 100ml (0.012g Sr / ml) of strontium nitrate aqueous solution for immersion for 24 hours, dry at 120°C for 12 hours, and then roast at 400°C for 3 hours to obtain rare earth modified Composite alumina carrier.
[0034] Put the above-mentioned pretreated carriers into 125ml of mixed aqueous solution containing ruthenium chloride and rhodium chloride respectively, wherein the Ru content is 0.002g / m1, and the Rh content is 0.0004g / ml, after soaking for 24 hours, dry at 120°C for 6 hours, repeat The above operations were performed 4 times, and after drying, they were calcined at 400°C for 4 hours to obtain the corresponding catalysts H-1, H-2, H-3, H-4, H-5, H-6, and H-7, loaded with 1% Ru and 0.2% Rh.
Embodiment 3
[0036] Tetrabutyl pyromellitic acid was dissolved in butanol to form a butanol solution containing 23% (wt) tetrabutyl pyromellitic acid, which was used as a reaction raw material solution. Load the catalyst in a single-tube fixed-bed reactor, reduce and activate it under a hydrogen atmosphere at a programmed temperature rise, and feed the raw material solution into the reactor through a metering pump for hydrogenation reaction. Reaction conditions: pressure 6.0Mpa, bed temperature 220 ℃, liquid space velocity 4.0h 1(V), hydrogen air velocity 250h 1 (V), after the hydrogenation mixed product is cooled, obtain the mixed product of the hydrogenated tetrabutylpyromellitic acid containing solvent butanol, carry out chromatographic analysis, as follows:
[0037] Table 2 Catalyst Activity Evaluation
[0038] catalyst Conversion rates(%) selectivity (%) H-1 99.6 98.4 H-2 99.1 98.0 H-3 99.4 98.2 H-4 99.0 9.6 H-5 ...
PUM
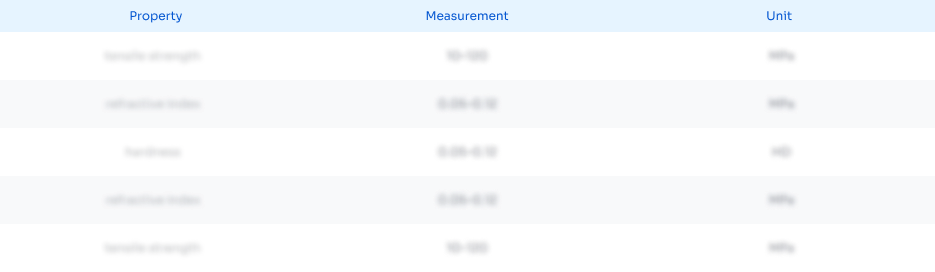
Abstract
Description
Claims
Application Information

- R&D Engineer
- R&D Manager
- IP Professional
- Industry Leading Data Capabilities
- Powerful AI technology
- Patent DNA Extraction
Browse by: Latest US Patents, China's latest patents, Technical Efficacy Thesaurus, Application Domain, Technology Topic, Popular Technical Reports.
© 2024 PatSnap. All rights reserved.Legal|Privacy policy|Modern Slavery Act Transparency Statement|Sitemap|About US| Contact US: help@patsnap.com