Copper-zinc-tin-sulfur or copper-zinc-tin-selenium target for absorbed layer of thin-film solar battery, preparation method for target and application of target
A copper-zinc-tin-selenium thin film and solar cell technology, applied in chemical instruments and methods, circuits, tin compounds, etc., can solve problems such as poor process stability, difficult film preparation, and complicated control of process parameters, and achieve improved efficiency and porosity The effect of low and high density
- Summary
- Abstract
- Description
- Claims
- Application Information
AI Technical Summary
Problems solved by technology
Method used
Image
Examples
Embodiment 1
[0022] Take Cu 2 S, ZnS, SnS 2The powder is used as the raw material, weighed at a molar ratio of 1:1:1, added deionized water or absolute ethanol as a ball milling medium, and mixed and ball milled at a speed of 350 r / min for 8 hours using a planetary ball mill. Dry the powder after ball milling, then put it into a high-temperature furnace with argon gas at atmospheric pressure for solid-phase synthesis reaction, raise the temperature to 400-700 degrees at a rate of 3 degrees per minute, keep it warm for 2 hours, and then cool naturally to room temperature. The reacted powder was ball-milled for 8 hours for the second time, and dried for later use. The powder after high-temperature synthesis and secondary ball milling is put into a steel mold, and subjected to axial pressure molding to obtain a biscuit. Finally, put the pressed green body into the sintering furnace, fill it with an inert gas such as argon or nitrogen at an atmospheric pressure, raise it to 700-800°C at a r...
Embodiment 2
[0024] Take Cu 2 S, ZnS, SnS 2 The powder is used as the raw material, weighed at a molar ratio of 1:1:1, added deionized water or absolute ethanol as a ball milling medium, and mixed and ball milled at a speed of 350 r / min for 8 hours using a planetary ball mill. Dry the powder after ball milling, then put it into a high-temperature furnace with argon gas at atmospheric pressure for solid-phase synthesis reaction, raise the temperature to 400-700 degrees at a rate of 3 degrees per minute, keep it warm for 2 hours, and then cool naturally to room temperature. The reacted powder was ball-milled for 8 hours for the second time, and dried for later use. Put the powder after high-temperature synthesis and secondary ball milling into a steel mold for axial pressure preforming. The preformed green body is tightly wrapped and molded under 200MPa isostatic pressure to obtain the final green body. Then the target is sintered according to the sintering method of Example 1.
Embodiment 3
[0026] Take Cu 2 S, ZnS, SnS 2 The powder is used as the raw material, weighed at a molar ratio of 1:1:1, added deionized water or absolute ethanol as a ball milling medium, and mixed and ball milled at a speed of 350 r / min for 8 hours using a planetary ball mill. Dry the powder after ball milling, then put it into a high-temperature furnace with argon gas at atmospheric pressure for solid-phase synthesis reaction, raise the temperature to 400-700 degrees at a rate of 3 degrees per minute, keep it warm for 2 hours, and then cool naturally to room temperature. The reacted powder was ball-milled for 8 hours for the second time, and dried for later use. Put the powder after high-temperature synthesis and secondary ball milling into a hot-press sintering mold, fill it with an inert gas (argon or nitrogen, etc.) Raise the heating rate to 700-800 degrees per minute, keep the temperature for 2 hours, then cool down to room temperature with the furnace, take it out after pressure r...
PUM
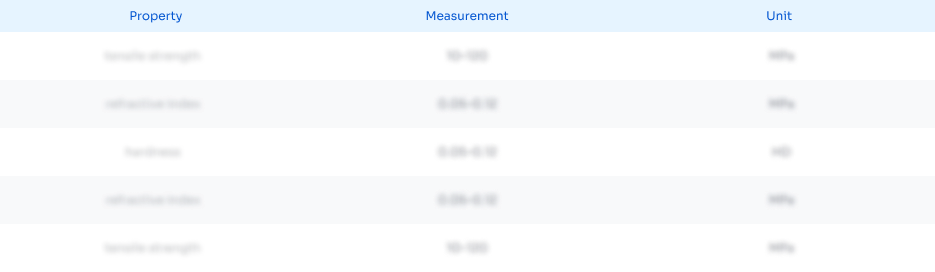
Abstract
Description
Claims
Application Information

- R&D Engineer
- R&D Manager
- IP Professional
- Industry Leading Data Capabilities
- Powerful AI technology
- Patent DNA Extraction
Browse by: Latest US Patents, China's latest patents, Technical Efficacy Thesaurus, Application Domain, Technology Topic, Popular Technical Reports.
© 2024 PatSnap. All rights reserved.Legal|Privacy policy|Modern Slavery Act Transparency Statement|Sitemap|About US| Contact US: help@patsnap.com