Method for deep reduction and magnetic separation of nickel and iron in lateritic nickel ore carbon-containing pellets
A technology of laterite nickel ore and carbon pellets, applied in chemical instruments and methods, wet separation, solid separation, etc., can solve the problems of low economic value, low production efficiency of scaling and corrosion, environmental pollution, etc., and the effect is obvious , chemical composition and physical properties are uniform and stable, and the effect of reducing production costs
- Summary
- Abstract
- Description
- Claims
- Application Information
AI Technical Summary
Problems solved by technology
Method used
Examples
Embodiment Construction
[0023] Grinding fineness has a great influence on the result. Stage grinding can be used, and the grinding fineness of laterite nickel ore is 0.074mm, accounting for 80% of the best; the grinding fineness of wet mill is 0.043mm, accounting for 95% of the best. After the material is lubricated and ground, the physical and chemical characteristics of the material are changed by the action of mechanical force, which can shorten the pelletizing time, reduce the amount of binder, and improve the falling strength of the green ball, but reduce the breaking temperature of the green ball. The specific surface area of the material after wetting is increased, the ball forming performance is good, and the particles are in an unstable high-energy state, thereby increasing the activity and improving the adsorption capacity of its surface. After grinding, the morphology of the particles is mostly needle-like, flake-like and strip-like, and there are cracks. The bridging mechanical interloc...
PUM
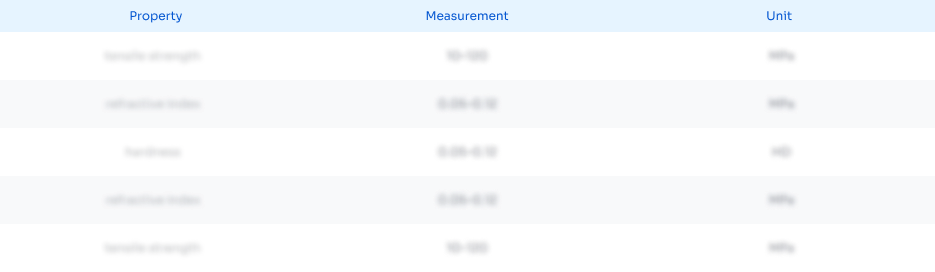
Abstract
Description
Claims
Application Information

- Generate Ideas
- Intellectual Property
- Life Sciences
- Materials
- Tech Scout
- Unparalleled Data Quality
- Higher Quality Content
- 60% Fewer Hallucinations
Browse by: Latest US Patents, China's latest patents, Technical Efficacy Thesaurus, Application Domain, Technology Topic, Popular Technical Reports.
© 2025 PatSnap. All rights reserved.Legal|Privacy policy|Modern Slavery Act Transparency Statement|Sitemap|About US| Contact US: help@patsnap.com