Process for removing acid gas from flue gas by using residual heat of flue gas
An acid gas and flue gas technology, applied in gas treatment, climate sustainability, greenhouse gas capture, etc., which can solve the problems of wasting latent heat and not meeting energy saving
- Summary
- Abstract
- Description
- Claims
- Application Information
AI Technical Summary
Problems solved by technology
Method used
Image
Examples
Embodiment 1
[0025] Now deal with the flue gas, in terms of volume fraction, it contains CO 2 is 13.98%, O 2 3.49%, N 2 72.87%, SO 2 0.21%, H 2 O is 9.45%, and the flue gas volume is 1,124,980 m 3 / h, the flue gas temperature is 300°C. It can be seen from the above content that since it does not contain nitrogen oxides and contains SO 2 and CO 2 Acid gas, need desulfurization absorption tower T1 and CO 2 Absorption tower T3 and CO 2 The regeneration tower T4 does not need the denitrification absorption tower T2. The flue gas enters the heat exchanger E1 through the pipeline 2, so that the temperature of the flue gas is reduced from 300°C to 120°C, and the water is heated at the same time, and the mixture of water vapor and liquid water obtained enters the phase separator V1, and the water returns after phase separation Heat exchanger E1 recirculates. The steam is divided into two streams through the splitter S1, one stream is used as a heating source, and the steam is converted i...
Embodiment 2
[0027] Now deal with the flue gas, in terms of volume fraction, it contains CO 2 7.6%, O 2 10%, N 2 54%, H 2 O is 28%, containing SO per cubic meter 3 Mass 1500 mg, containing NO X Mainly NO, 1200 mg, flue gas volume 12000 m 3 / h, the flue gas temperature is 300°C. It can be seen from the above content that due to the nitrogen oxides, SO 2 and CO 2 Acid gas, need desulfurization absorption tower T1, denitrification tower to absorb T2, CO 2 Absorption tower T3 and CO 2 Regeneration tower T4. First pass the flue gas through the heat exchanger E1, so that the temperature of the flue gas is reduced from 300°C to 120°C, and at the same time, the water from the pipeline 1 through the mixer M1 is heated after passing through the heat exchanger E1, and the heated water and steam The mixture enters the phase separator V1, and the liquid water after phase separation returns to the heat exchanger E1 through the mixer M1 for recycling. After the phase separation, the water vapo...
Embodiment 3
[0030] Now deal with the flue gas, in terms of volume fraction, it contains CO 2 is 12.06%, O 2 10.1%, N 2 60.54%, SO 2 0.12%, NOx 0.1%, H 2 O is 17.08%, and the flue gas volume is 1,442,650 m 3 / h, the flue gas temperature is 415°C. It can be seen from the above content that due to the nitrogen oxides, SO 2 and CO 2 For acidic gas, desulfurization absorption tower T1, denitrification absorption tower T2, CO 2 Absorption tower T3 and CO 2 Regeneration tower T4. First pass the flue gas through the heat exchanger IE1, so that the temperature of the flue gas is reduced from 415 ° C to 120 ° C, and at the same time, the water from the pipeline 1 through the mixer M1 is heated after passing through the heat exchanger E1, and the heated water and steam The mixture enters the phase separator V1, and the liquid water after phase separation returns to the heat exchanger IE1 for recycling through the mixer M1. After the phase separation, the water vapor is divided into three s...
PUM
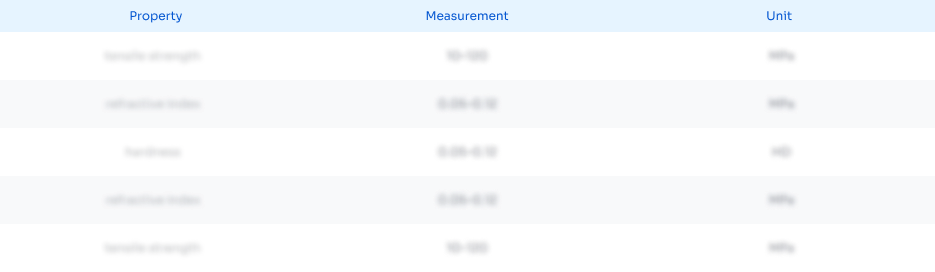
Abstract
Description
Claims
Application Information

- Generate Ideas
- Intellectual Property
- Life Sciences
- Materials
- Tech Scout
- Unparalleled Data Quality
- Higher Quality Content
- 60% Fewer Hallucinations
Browse by: Latest US Patents, China's latest patents, Technical Efficacy Thesaurus, Application Domain, Technology Topic, Popular Technical Reports.
© 2025 PatSnap. All rights reserved.Legal|Privacy policy|Modern Slavery Act Transparency Statement|Sitemap|About US| Contact US: help@patsnap.com