Steel-making method of experimental induction furnace
An induction furnace, a technology used in experiments, applied in the field of steelmaking, to achieve the effect of eliminating the erosion of the furnace lining, flexible and effective operation, and eliminating pollution
- Summary
- Abstract
- Description
- Claims
- Application Information
AI Technical Summary
Problems solved by technology
Method used
Examples
Embodiment 1
[0034] 61Kg of solid metal material is loaded into the intermediate frequency induction furnace to smelt low-carbon and low-phosphorus steel, and the output power of the power supply during the smelting process is 30-45 kilowatts. Its experimental steelmaking steps:
[0035] 1) Power on to completely melt the solid metal material in the furnace;
[0036] 2) A water-cooled oxygen lance is used to blow oxygen from the top of the furnace into the furnace. During the blowing process, the position of the oxygen lance is fixed at 40% of the oxygen lance nozzle from the static depth of the molten steel, and the oxygen supply intensity is 3.1Nm per ton of steel. 3 / min, while blowing in nitrogen gas from the gas supply element at the bottom of the furnace to stir, the gas supply intensity is 0.05-0.10Nm per ton of steel 3 / min;
[0037] 3) Slagging: lime and dolomite are used, and the addition amount is lime 50kg / ton steel and dolomite 16kg / ton steel;
[0038] 4) When the top oxyge...
Embodiment 2
[0043] 60Kg of solid metal material is loaded into the intermediate frequency induction furnace to smelt low-carbon steel, and the output power of the power supply during the smelting process is 20-40 kilowatts. Its experimental steelmaking steps:
[0044] 1) Power on to completely melt the solid metal material in the furnace;
[0045]2) The water-cooled oxygen lance is used to blow oxygen from the furnace top to the furnace. The position of the oxygen lance is fixed at 45% of the oxygen lance nozzle from the resting depth of molten steel during the blowing process, and the oxygen supply intensity is 3.3m per ton of steel. 3 / min, while argon is blown into the gas supply element from the bottom of the furnace to stir, and the gas supply intensity is 0.08-0.15Nm per ton of steel 3 / min;
[0046] 3) Slagging: lime and dolomite are used, and the addition amount is lime 52kg / ton steel and dolomite 18kg / ton steel;
[0047] 4) When the top oxygen blowing time reaches 16 minutes, ...
Embodiment 3
[0052] 60Kg of solid metal material is loaded into the intermediate frequency induction furnace to smelt low-carbon and low-phosphorus steel, and the output power of the power supply during the smelting process is 30-45 kilowatts. Its experimental steelmaking steps:
[0053] 1) Power on to completely melt the solid metal material in the furnace;
[0054] 2) The water-cooled oxygen lance is used to spray oxygen from the furnace top into the furnace, and the operation of lowering the position of the oxygen lance during the blowing process is carried out in the following manner: 50% at the still depth of molten steel for 0.5min, and 50% at the still depth of molten steel for 5.5min 60%, 70% of the static depth of molten steel at the end of oxygen blowing; the oxygen supply intensity is 3.3Nm per ton of steel 3 / min;
[0055] 3) Slagging: Lime, dolomite and fluorite are used, and the addition amount is lime 53kg / ton steel, dolomite 18kg / ton steel, fluorite 4.5kg / ton steel;
[0...
PUM
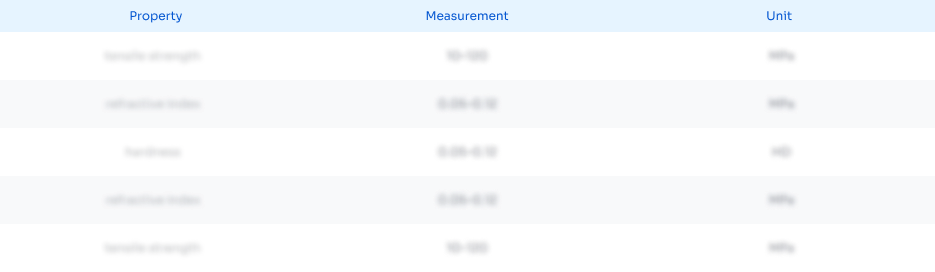
Abstract
Description
Claims
Application Information

- R&D Engineer
- R&D Manager
- IP Professional
- Industry Leading Data Capabilities
- Powerful AI technology
- Patent DNA Extraction
Browse by: Latest US Patents, China's latest patents, Technical Efficacy Thesaurus, Application Domain, Technology Topic, Popular Technical Reports.
© 2024 PatSnap. All rights reserved.Legal|Privacy policy|Modern Slavery Act Transparency Statement|Sitemap|About US| Contact US: help@patsnap.com