Method for extracting metal from high calcium metal slag
A technology for extracting metal and metal slag, applied in the field of metallurgy, can solve the problems of low metal desulfurization rate, tight thermal balance, small amount of steel-making slag, etc., and achieves the effects of broad application prospects, low cost and simple process
- Summary
- Abstract
- Description
- Claims
- Application Information
AI Technical Summary
Problems solved by technology
Method used
Examples
example 1
[0032] Example 1 adopts the inventive method to extract vanadium, chromium from high calcium vanadium slag
[0033] 1. Test raw materials
[0034] (1) The chemical composition of high calcium vanadium slag is shown in Table 1;
[0035] Table 1 Chemical composition of high calcium vanadium slag (wt%)
[0036] Element
V 2 o 5
CaO
SiO 2
Cr 2 o 3
P
S
TF
content
7.56
12.76
13.2
1.6
0.12
0.14
23.54
[0037] (2) The roasting additive is industrial pure sodium aluminate.
[0038] 2. Test method
[0039] (1) Ingredients
[0040] V in vanadium slag 2 o 5 content with sodium aluminate, converted to Na 2 O / V 2 o 5 The weight ratio was 0.8.
[0041] (2) Roasting temperature and time
[0042] The prepared roasted material is oxidized and roasted in the furnace, and the temperature is evenly raised to 700°C after 90 minutes, and it is kept for 6 hours before being released f...
example 2
[0045] Example 2 adopts the inventive method to extract vanadium, chromium from high calcium vanadium slag
[0046] 1. Test raw materials
[0047] (1) The chemical composition of high calcium vanadium slag is shown in Table 1;
[0048] (2) The roasting additive is industrial pure sodium aluminate.
[0049] 2. Test method
[0050] (1) Ingredients
[0051] V in vanadium slag 2 o 5 content with sodium aluminate, converted to Na 2 O / V 2 o 5 The weight ratio is 1.0.
[0052] (2) Roasting temperature and time
[0053] The prepared roasted material is oxidized and roasted in the furnace, and the temperature is evenly raised to 850°C after 90 minutes, and it is kept for 4 hours before being released from the furnace.
[0054] (3) Leaching: leaching time 60min, liquid: solid = 4:1, temperature 95°C.
[0055] Results: The vanadium leaching rate was 90wt%, and the chromium leaching rate was 91wt%.
example 3
[0056] Example 3 adopts the inventive method to extract vanadium, chromium from high calcium vanadium slag
[0057] 1. Test raw materials
[0058] (1) The chemical composition of high calcium vanadium slag is shown in Table 1;
[0059] (2) The roasting additive is industrial pure sodium aluminate.
[0060] 2. Test method
[0061] (1) Ingredients
[0062] V in vanadium slag 2 o 5 content with sodium aluminate, converted to Na 2 O / V 2 o 5 The weight ratio is 1.2.
[0063] (2) Roasting temperature and time
[0064] The prepared roasted material is oxidized and roasted in the furnace, and the temperature is evenly raised to 1000°C after 90 minutes, and it is kept for 2 hours before being released from the furnace.
[0065] (3) Leaching: leaching time 60min, liquid: solid = 4:1, temperature 95°C.
[0066] Results: The vanadium leaching rate was 92wt%, and the chromium leaching rate was 93wt%.
PUM
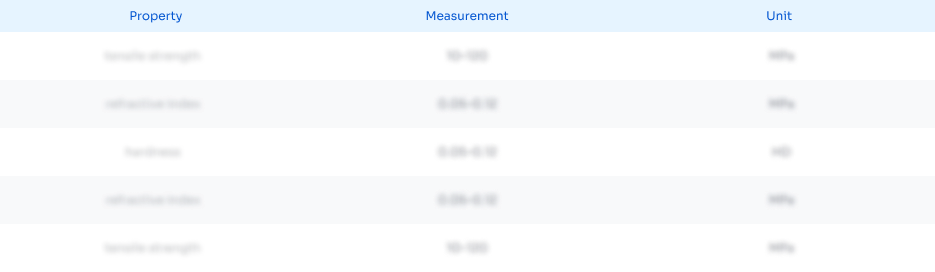
Abstract
Description
Claims
Application Information

- R&D Engineer
- R&D Manager
- IP Professional
- Industry Leading Data Capabilities
- Powerful AI technology
- Patent DNA Extraction
Browse by: Latest US Patents, China's latest patents, Technical Efficacy Thesaurus, Application Domain, Technology Topic, Popular Technical Reports.
© 2024 PatSnap. All rights reserved.Legal|Privacy policy|Modern Slavery Act Transparency Statement|Sitemap|About US| Contact US: help@patsnap.com