Manufacturing method of isolation board for sintering
A manufacturing method and technology for isolating plates, which are applied in the field of plate blank sintering, can solve the problems of metal plate deformation, contact surface damage, and high thermal spraying process cost, and achieve the effects of preventing sintering adhesion, high production efficiency and simple process.
- Summary
- Abstract
- Description
- Claims
- Application Information
AI Technical Summary
Problems solved by technology
Method used
Examples
Embodiment 1
[0016] (1) Slurry preparation: prepare polyvinyl alcohol into an aqueous solution with a mass percentage concentration of 2%, then add alumina powder (or zirconia powder) to the prepared aqueous solution, and stir evenly at 50°C to obtain a slurry , the amount of alumina powder (or zirconia powder) added is 50g per liter of aqueous solution;
[0017] (2) brush coating slurry: adopt the flat metal plate (stainless steel plate) of surface, evenly coat the slurry described in the step (1) on one side of the metal plate, make the slurry cover the surface of the metal plate completely during coating;
[0018] (3) Drying: putting the metal plate coated with the slurry in step (2) into an oven (the temperature is controlled between 80° C. and 110° C.) to dry to obtain a separator for sintering.
[0019] The isolation plate manufactured in this embodiment is an isolation plate that is in contact with the sintered plate blank on one side and functions as isolation between the bottom an...
Embodiment 2
[0021] (1) Slurry preparation: prepare polyvinyl alcohol into an aqueous solution with a concentration of 10% by mass, then add zirconia powder (or alumina powder) to the prepared aqueous solution, and stir evenly at 80°C to obtain a slurry , the amount of zirconia powder (or alumina powder) added is 100g per liter of aqueous solution;
[0022] (2) brush coating slurry: adopt the flat metal plate (stainless steel plate) of surface, evenly coat the slurry described in the step (1) on both sides of the metal plate, make the slurry cover the surface of the metal plate completely during coating;
[0023] (3) Drying: putting the metal plate coated with the slurry in step (2) into an oven (the temperature is controlled between 80° C. and 110° C.) to dry to obtain a separator for sintering.
[0024] The separator made in this embodiment is a separator whose two sides are in contact with the sintered blanks and serves as a separator between the sintered blanks during sintering. When ...
Embodiment 3
[0026] (1) Slurry preparation: prepare polyvinyl alcohol into an aqueous solution with a mass percent concentration of 6%, then add zirconia powder (or alumina powder) to the prepared aqueous solution, and stir evenly at 100°C to obtain a slurry , the total amount of zirconia powder (or aluminum oxide powder) added is 150g per liter of aqueous solution;
[0027] (2) brush coating slurry: adopt the flat metal plate (stainless steel plate) of surface, evenly coat the slurry described in the step (1) on one side of the metal plate, make the slurry cover the surface of the metal plate completely during coating;
[0028] (3) Drying: putting the metal plate coated with the slurry in step (2) into an oven (the temperature is controlled between 80° C. and 110° C.) to dry to obtain a separator for sintering.
[0029] The isolation plate manufactured in this embodiment is an isolation plate that is in contact with the sintered plate blank on one side and functions as isolation between t...
PUM
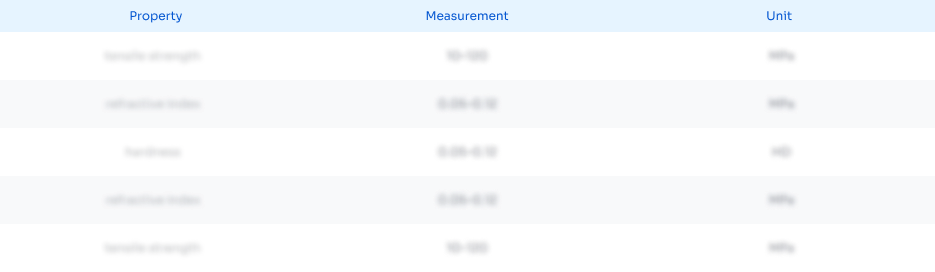
Abstract
Description
Claims
Application Information

- Generate Ideas
- Intellectual Property
- Life Sciences
- Materials
- Tech Scout
- Unparalleled Data Quality
- Higher Quality Content
- 60% Fewer Hallucinations
Browse by: Latest US Patents, China's latest patents, Technical Efficacy Thesaurus, Application Domain, Technology Topic, Popular Technical Reports.
© 2025 PatSnap. All rights reserved.Legal|Privacy policy|Modern Slavery Act Transparency Statement|Sitemap|About US| Contact US: help@patsnap.com