Reciprocating type porous medium gas burning metal smelting furnace
A porous medium and reciprocating technology, applied in furnaces, crucible furnaces, furnace components, etc., can solve the problems of high combustion efficiency and energy utilization, low pollution emissions, etc., and achieve high combustion efficiency and energy utilization, The effect of low pollution emission and high combustion intensity
- Summary
- Abstract
- Description
- Claims
- Application Information
AI Technical Summary
Problems solved by technology
Method used
Image
Examples
Embodiment 1
[0028] like figure 1 , the first air flue gas channel 1, the first gas inlet pipe 2, the blower 3, the air supply channel 4, the first gas control valve 5, the air flue gas reversing valve 6, the flue gas flow channel 7, the induced draft fan 8 , the second gas control valve 9, the thermocouple 10, the second gas inlet pipe 11, the second air flue flow channel 12, the controller 13, the second porous medium regenerator 14, the second gas high-temperature air mixing chamber 15 , the second gas air inlet perforated plate 16, the third gas inlet pipe 17, the flame detector 18, the high-energy electronic igniter 19, the third gas control valve 20, the fourth gas control valve 21, the ignition gas control valve 22, the fourth Gas inlet pipe 23 , first gas high temperature air mixing chamber 25 , first gas air inlet perforated plate 24 , first porous medium heat storage chamber 26 .
[0029] like figure 2 , Smelting gas removal device 27, metal holding container 28, combustion ch...
Embodiment 2
[0042] Refer to attached figure 1 , 2 , 5(a), 5(b):
[0043] The difference between this embodiment and Embodiment 1 is that the arrangement of the first porous medium heat storage chamber and the second porous medium heat storage chamber is arranged in the same direction, and the second porous medium heat storage chamber 14 and the first porous medium heat storage chamber The included angle β between the heat storage chambers 26≤20°.
[0044] The rest is the same.
Embodiment 3
[0046] Refer to attached figure 1 , 2 , 3, 4(a), 4(b):
[0047] The difference between the present embodiment and the first embodiment lies in that the air path setting of the periodically reversing air supply mechanism is different.
[0048] like image 3 As shown, the air and gas reversing valve 6 can adopt a 4-way control valve system. In the first half cycle, the second air and flue gas reversing valve 32 and the fourth air and flue gas reversing valve 34 are opened, and the first air and flue gas reversing valve 31 and the third air and flue gas reversing valve 33 are closed; The second air and smoke reversing valve 32 and the fourth air and smoke reversing valve 34 are closed, and the first air and smoke reversing valve 31 and the third air and smoke reversing valve 33 are opened.
[0049] The rest is the same.
PUM
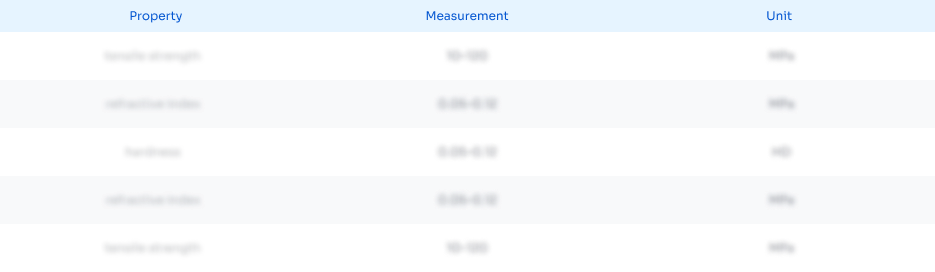
Abstract
Description
Claims
Application Information

- Generate Ideas
- Intellectual Property
- Life Sciences
- Materials
- Tech Scout
- Unparalleled Data Quality
- Higher Quality Content
- 60% Fewer Hallucinations
Browse by: Latest US Patents, China's latest patents, Technical Efficacy Thesaurus, Application Domain, Technology Topic, Popular Technical Reports.
© 2025 PatSnap. All rights reserved.Legal|Privacy policy|Modern Slavery Act Transparency Statement|Sitemap|About US| Contact US: help@patsnap.com