Preparation method of silicon-free calcium and iron-containing alloy
A ferroalloy and alloy technology, which is applied in the field of preparation of silicon-free calcium-containing ferroalloy, can solve the problems of large calcium burning loss and low calcium content in the alloy
- Summary
- Abstract
- Description
- Claims
- Application Information
AI Technical Summary
Problems solved by technology
Method used
Examples
Embodiment 1
[0020] Example 1, a calcium-aluminum-iron alloy was prepared with a semi-closed 350KVA intermediate frequency electric furnace, and the alloy composition was Ca 15%, Al 40%, and the balance was Fe. The total charge in the furnace is 200kg, including 32kg of calcium metal, 81kg of aluminum metal and 87kg of steel scrap. The invention uses the metal remelting method to prepare silicon-free and calcium-containing ferroalloy, puts the above-mentioned charge into the furnace, and starts smelting through power transmission. In the furnace for 15 minutes, when the melting temperature is about 400°C, cover the furnace cover, burn the sundries in the charge (scrap steel), input liquefied gas into the furnace from the feeding port with a conduit, ignite in the closed space in the furnace, and Inject inert gas into the furnace to make the oxygen content in the furnace gas reach 6%. In about 45 minutes, the furnace temperature reaches 1350°C, and all the raw materials in the furnace are ...
Embodiment 2
[0021] Example 2, using the electric furnace of implementation 1 to produce calcium-aluminum-manganese-ferroalloy, the target composition of the alloy is 30% Ca, 30% Al, 30% Mn, and the balance is Fe. Prepare 200kg of charge, including 64kg of calcium, 62kg of metal aluminum, 40kg of medium carbon ferromanganese (containing Mn75%), and 34kg of scrap steel. Put the above-mentioned raw materials into the furnace and send electricity to start smelting. After 15 minutes, the furnace cover was put on. When the melting temperature in the furnace reached 400°C, the oxygen content in the gas in the furnace was detected to be about 7%, and there was still burning phenomenon. Add 1.5kg of mixed flame retardants such as chlorinated paraffin, sulfur, and calcium oxide to assist in flame retardancy. In 43 minutes, the furnace temperature reached 1300°C, and the alloy was completely melted. Open the closed door of the casting chamber before coming out of the furnace, put the mould, and cl...
Embodiment 3
[0022]Example 3, using the electric furnace of Example 1 to produce calcium-magnesium-iron alloys, the alloy target composition is Ca 40%, Mg 5%, and the balance is Fe. Furnace charge ratio metal calcium 82kg, metal magnesium 10kg, scrap steel 108kg, a total of 200kg. Put the above charge into the electric furnace, and start smelting with electricity. After 15 minutes, when the furnace temperature reaches 400°C, cover the furnace cover, and detect that the oxygen content in the gas is 8%, and there is combustion in the furnace. It is still higher than 5%, and inert gas is added to reduce the oxygen content to below 5%, so that there is no combustion in the furnace. In order to prevent calcium burning, it can be combined with argon injection into the furnace. The amount of argon injection depends on the degree of no combustion in the furnace. After 40 minutes, the temperature in the furnace reached 1250°C, and the alloy was completely melted. Put the mold in the casting room...
PUM
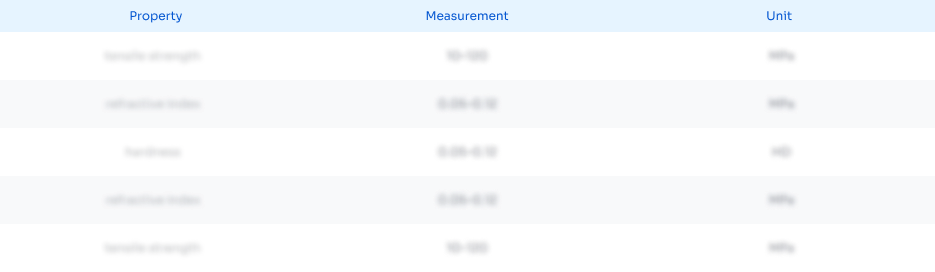
Abstract
Description
Claims
Application Information

- R&D
- Intellectual Property
- Life Sciences
- Materials
- Tech Scout
- Unparalleled Data Quality
- Higher Quality Content
- 60% Fewer Hallucinations
Browse by: Latest US Patents, China's latest patents, Technical Efficacy Thesaurus, Application Domain, Technology Topic, Popular Technical Reports.
© 2025 PatSnap. All rights reserved.Legal|Privacy policy|Modern Slavery Act Transparency Statement|Sitemap|About US| Contact US: help@patsnap.com