Catalytic cracking catalyst and preparation method thereof
A catalytic thermal cracking and catalyst technology, which is applied in catalytic cracking, physical/chemical process catalysts, molecular sieve catalysts, etc., can solve problems such as unsatisfactory effects, and achieve good anti-calcium pollution performance, good sphericity, and high ethylene yield. Effect
- Summary
- Abstract
- Description
- Claims
- Application Information
AI Technical Summary
Problems solved by technology
Method used
Image
Examples
example 1
[0031] (1) 17.0Kg halloysite (industrial product of Suzhou China Clay Company, solid content 72.3% by weight) was roasted at 800° C. for 1.5 hours, then mixed with 48.0 Kg decationized water, beating to obtain kaolin slurry;
[0032] (2) 20Kg decationized water is mixed with 11.9Kg pseudo-boehmite (industrial product of Shandong Aluminum Plant, solid content 63m%), beating, and its pH value is adjusted to 3 with hydrochloric acid;
[0033] (3) 5.19Kg of ZrOCl 2 (where ZrO 2 Content is 36% by weight, technical grade, product of Zibo Huantuo Chemical Co., Ltd.) and deionized water are mixed to prepare ZrOCl 2 Concentration is the solution of 1.0mol / L, add ammoniacal liquor (Beijing Chemical Plant, concentration 25% by weight) under stirring to pH value 9, then aged 26 hours at 25 ℃, under stirring, filter to get ZrO(OH) 2 Gel, washed with deionized water until no Cl was detected in the washing solution after washing - , dried at 120°C for 24 hours, and calcined at 550°C for 2...
example 2
[0040] (1) Get 11.4Kg hallowed kaolin (industrial product of Suzhou China Clay Company, solid content 72.3% by weight) and roast at 700°C for 2 hours, mix with 48.0Kg decationized water, beating, and make kaolin slurry.
[0041] (2) 20Kg decationized water is mixed with 11.9Kg pseudo-boehmite (industrial product of Shandong Aluminum Plant, solid content 63m%), beating, and its pH value is adjusted to 2.5 with hydrochloric acid;
[0042] (3) 6.87Kg zirconium oxychloride (zirconia content is 36% by weight, industrial grade, Zibo Huantuo Chemical Co., Ltd.) is mixed with deionized water to make ZrOCl 2 A solution with a concentration of 1.5 mol / L, under stirring, was added ammonia water (Beijing Chemical Plant, 25% by weight) to a pH value of 10, then aged at 30°C for 16 hours with stirring, and filtered to obtain ZrO(OH) 2 Gel, washed with deionized water until Cl-free in the washed water - Detected, dried at 115°C for 26 hours, and calcined at 600°C for 5 hours to obtain 2.47 ...
Embodiment 3~4
[0054] On a small-scale fixed fluidized bed device, take 30m% residual oil + 70m% wax oil (see Table 2 for properties) as raw material, and add iron naphthenate to it, so that 0.5% by mass of iron is contained in the raw material oil, and the catalyst sample A~B were evaluated, the reaction temperature was 640°C, the weight ratio of agent to oil was 15, the mass ratio of water to oil was 35:1, and the weight hourly space velocity was 10h -1 . The catalyst sample was treated with 100% steam at 800°C for 17 hours in advance, and the loading amount was 240 grams. The evaluation results are shown in Table 3.
PUM
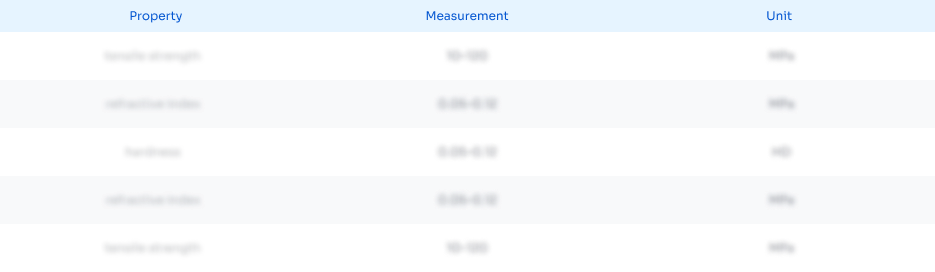
Abstract
Description
Claims
Application Information

- R&D
- Intellectual Property
- Life Sciences
- Materials
- Tech Scout
- Unparalleled Data Quality
- Higher Quality Content
- 60% Fewer Hallucinations
Browse by: Latest US Patents, China's latest patents, Technical Efficacy Thesaurus, Application Domain, Technology Topic, Popular Technical Reports.
© 2025 PatSnap. All rights reserved.Legal|Privacy policy|Modern Slavery Act Transparency Statement|Sitemap|About US| Contact US: help@patsnap.com