Anti-icing composite coating and manufacturing method thereof
A composite coating, anti-icing technology, applied in the directions of coatings, chemical instruments and methods, synthetic resin layered products, etc. Focus on problems such as force, to achieve the effect of reducing adhesion, low surface tension, and low cost
- Summary
- Abstract
- Description
- Claims
- Application Information
AI Technical Summary
Problems solved by technology
Method used
Examples
Embodiment 1
[0019] Inner layer - preparation of silicone-modified epoxy resin: Add 100 mL of diethyl ether, 13.2 g of HSi(OCH 3 ) 3 , stirred, and added 20.3 g of glycidyl alcohol and 30.3 g of triethylamine at 0° C., and raised the temperature to 30° C. for 8 hours. Stop stirring, filter, and separate to obtain a colorless silicone-modified epoxy resin liquid.
[0020] Preparation of the outer layer-fluorosilicon-modified acrylate: In a 250 mL three-neck flask, add 60 g of water and 0.2 g of sodium lauryl sulfate in sequence, and stir. Then 0.5 g vinyltriethoxysilane, 10.0 g hexafluorobutyl methacrylate, 5.0 g methyl methacrylate, and 0.15 g benzoyl peroxide were mixed together, ultrasonicated for 10 min, and then added to the three-necked flask Medium, N 2 protected, heated to 75°C, and reacted for 6 h to obtain a colorless transparent granular polymer. Take 15.0 g of the obtained polymer and 120 mL of ethanol, add them in turn to a 250 mL single-necked flask with a reflux tube, rai...
Embodiment 2
[0025] Inner layer - preparation of silicone-modified epoxy resin: In a 250 mL flask, add 150 mL THF, 13.2 g HSi(OCH 3 ) 3, stirred, and added 21.6 g epoxybutanol and 30.3 g triethylamine at 0°C, and heated to 60°C for 5 h. Stop stirring, filter, and separate to obtain a colorless silicone-modified epoxy resin liquid.
[0026] Preparation of the outer layer-fluorosilicon-modified acrylate: In a 250 mL three-necked flask, add 60 g of water and 0.2 g of sodium lauryl sulfate successively, and stir. Then 0.5 g vinyltriethoxysilane, 10.0 g hexafluorobutyl methacrylate, 5.0 g methyl methacrylate, and 0.15 g benzoyl peroxide were mixed together, ultrasonicated for 10 min, and then added to the three-necked flask Medium, N 2 protected, heated to 75°C, and reacted for 6 h to obtain a colorless transparent granular polymer. Take 15.0 g of the obtained polymer and 120 mL of ethanol, add them in turn to a 250 mL single-necked flask with a reflux tube, raise the temperature to 70 °C, ...
Embodiment 3
[0031] Inner layer - preparation of silicone-modified epoxy resin: Add 200 mL THF, 15.7 g Si(OCH 2 CH 3 ) 4 , stirred, added 23.2 g of glycidyl alcohol and 30.3 g of triethylamine at 0 °C, and heated to 50 °C for 3 h. Stop stirring, filter, and separate to obtain a colorless silicone-modified epoxy resin liquid.
[0032] Preparation of the outer layer-fluorosilicon-modified acrylate: In a 250 mL three-neck flask, add 60 g of water and 0.2 g of sodium lauryl sulfate in sequence, and stir. Then 0.5g of vinyltrimethoxysilane, 10.0g of trifluoroethyl methacrylate, 5.0g of methyl methacrylate, and 0.15g of benzoyl peroxide were mixed together, ultrasonicated for 10min, and then added to a three-necked flask. Under N2 protection, the temperature was raised to 75° C., and reacted for 6 hours to obtain a colorless transparent granular polymer. Take 15.0 g of the obtained polymer and 120 mL of ethanol, add them in turn to a 250 mL single-necked flask with a reflux tube, raise the t...
PUM
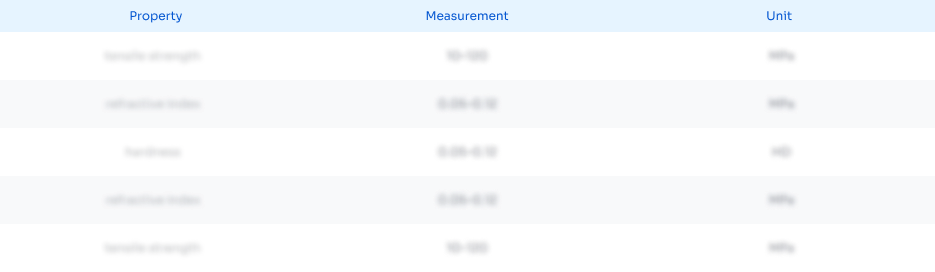
Abstract
Description
Claims
Application Information

- Generate Ideas
- Intellectual Property
- Life Sciences
- Materials
- Tech Scout
- Unparalleled Data Quality
- Higher Quality Content
- 60% Fewer Hallucinations
Browse by: Latest US Patents, China's latest patents, Technical Efficacy Thesaurus, Application Domain, Technology Topic, Popular Technical Reports.
© 2025 PatSnap. All rights reserved.Legal|Privacy policy|Modern Slavery Act Transparency Statement|Sitemap|About US| Contact US: help@patsnap.com