Anti-melting aluminum-silicon alloy corrosion gradient protective coating for solar thermal power generation, and preparation thereof
A technology of solar thermal power generation and protective coating, applied in metal material coating process, coating, melting spraying and other directions, can solve the problem of reducing the corrosion resistance of the coating to molten aluminum-silicon alloy, the high porosity of the coating, and the difference in thermal expansion coefficient. bigger problems
- Summary
- Abstract
- Description
- Claims
- Application Information
AI Technical Summary
Problems solved by technology
Method used
Image
Examples
Embodiment Construction
[0014] The sample size is 50mm×25mm×3mm, and the material is 310S. A low-pressure plasma spraying method is used to first spray a 60μm Co-based alloy buffer transition layer on the substrate, and after the buffer transition layer is cooled in the low-pressure chamber, the MoB / CoCr surface protective coating with a thickness of 130μm is sprayed. The spraying process parameters are as follows: walking gun speed is 600mm / s, power is 51KW, voltage is 73V, current is 698A, argon flow is 59l / min, hydrogen flow is 6l / min, powder feeding rate is 12rpm, pressure is 60torr, The spray distance is 200mm.
[0015] The sample after thermal spraying is used for thermal shock experiment. In the thermal shock experiment, the sample is heated to 700℃ and the whole is soaked, then the quenching water is taken out and cooled to room temperature; this procedure is repeated until cracks, peeling or peeling of the thermal spray coating on the surface appear, and finally record the occurrence The numb...
PUM
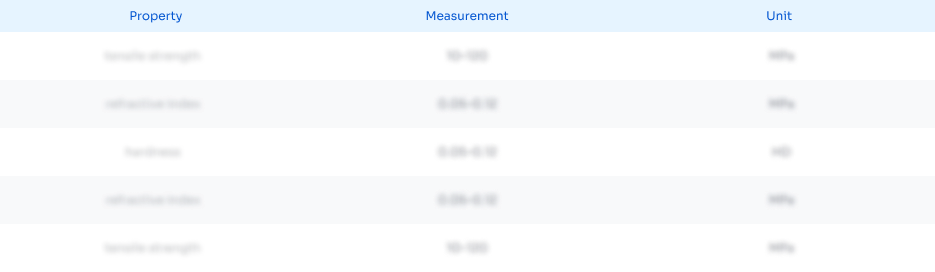
Abstract
Description
Claims
Application Information

- Generate Ideas
- Intellectual Property
- Life Sciences
- Materials
- Tech Scout
- Unparalleled Data Quality
- Higher Quality Content
- 60% Fewer Hallucinations
Browse by: Latest US Patents, China's latest patents, Technical Efficacy Thesaurus, Application Domain, Technology Topic, Popular Technical Reports.
© 2025 PatSnap. All rights reserved.Legal|Privacy policy|Modern Slavery Act Transparency Statement|Sitemap|About US| Contact US: help@patsnap.com