Process for manufacturing steel forge piece of vertical conveying pipe of deep sea oil extraction equipment
A manufacturing process and technology for steel forgings, which is applied in the field of steel forgings manufacturing process for deep-sea oil production equipment delivery risers, can solve the problems that the low-temperature toughness is difficult to meet the requirements and cannot be used in low-temperature working conditions, and achieves saving forging equipment occupancy rate, one-time delivery The effect of improving the inspection pass rate and reducing the number of upsets
- Summary
- Abstract
- Description
- Claims
- Application Information
AI Technical Summary
Problems solved by technology
Method used
Image
Examples
Embodiment (
[0059] Embodiment (process number C), the specific steps are as follows:
[0060] Step C①: Using chromium-molybdenum low-alloy steel as a blank, the chromium-molybdenum low-alloy steel blank is smelted by the process of primary smelting in an electric furnace, refining outside the furnace, and vacuum degassing. The chromium-molybdenum low-alloy steel is composed of carbon, silicon, manganese , chromium, molybdenum, phosphorus, sulfur, hydrogen, nickel, niobium, vanadium, titanium, copper and aluminum, its mass percentage is:
[0061] 0.12%≤carbon≤0.15%, 0.15%≤silicon≤0.40%, 0.50%≤manganese≤0.60%, 2.25%≤chromium≤2.50%, 1.00%≤molybdenum≤1.10%, phosphorus≤0.020%, sulfur≤0.015%, Hydrogen≤2.0ppm, 0.20%≤nickel≤0.50%, 0<niobium≤0.01%, 0<vanadium≤0.01%,
[0062] 0<titanium≤0.025%, 0<copper≤0.20%, 0<aluminum≤0.05%, and the total amount of titanium, copper and aluminum≤0.50%,
[0063] Step C②: Select the square ingot according to the size of the required structural parts, put it into ...
PUM
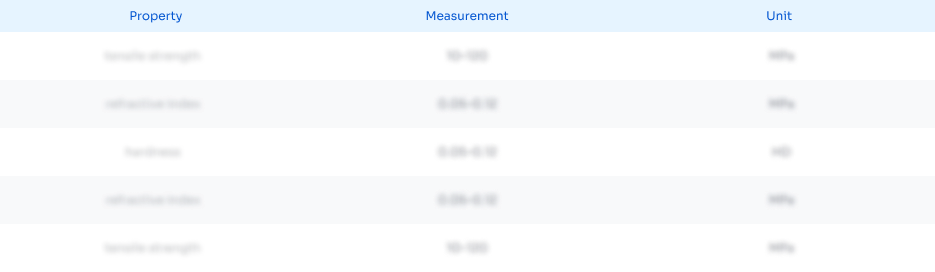
Abstract
Description
Claims
Application Information

- R&D Engineer
- R&D Manager
- IP Professional
- Industry Leading Data Capabilities
- Powerful AI technology
- Patent DNA Extraction
Browse by: Latest US Patents, China's latest patents, Technical Efficacy Thesaurus, Application Domain, Technology Topic, Popular Technical Reports.
© 2024 PatSnap. All rights reserved.Legal|Privacy policy|Modern Slavery Act Transparency Statement|Sitemap|About US| Contact US: help@patsnap.com