Method for extracting alumina from bauxite
A technology of bauxite and alumina, applied in chemical instruments and methods, aluminum compounds, inorganic chemistry, etc., can solve the problems of decreased extraction rate, long and complicated process, and large amount of slag discharge, and achieve energy consumption and production The effect of cost reduction, simple process, and lower grade requirements
- Summary
- Abstract
- Description
- Claims
- Application Information
AI Technical Summary
Problems solved by technology
Method used
Image
Examples
Embodiment 1
[0033] (1) Mix the crushed bauxite with solid sodium carbonate at a ratio of 1:0.6 and grind it into a 100-mesh mixed material.
[0034] (2) Calcining the mixed material obtained in step (1) at a temperature of 620° C. for 60 minutes to obtain roasted clinker. The roasted clinker is divided into several equal parts with the same quality for later use; during roasting, the roasting equipment is connected to the gas output pipe and connected to the carbon separation tank, and the recovered carbon dioxide gas is directly used for carbon separation.
[0035] (3) Add an appropriate amount of water to the first portion of roasted clinker, and make the solid-liquid mass ratio 1:6, and leaching for 50 minutes at a temperature of 10°C. After leaching, filter to obtain filter residue and filtrate respectively. After determination, the leaching rate of alumina in the filtrate was 76%, and the leaching rates of other components such as silicon dioxide and iron oxide were all zero.
[00...
Embodiment 2
[0043] (1) Mix the crushed bauxite with solid sodium carbonate at a ratio of 1:2.5 and grind it into a 250-mesh mixed material.
[0044] (2) Calcining the mixed material obtained in step (1) at a temperature of 990° C. for 10 minutes to obtain roasted clinker. The roasted clinker is divided into several equal parts with the same quality for later use; during roasting, the roasting equipment is connected to the gas output pipe and connected to the carbon separation tank, and the recovered carbon dioxide gas is directly used for carbon separation.
[0045] (3) Add an appropriate amount of water to the first portion of roasted clinker, and make the solid-to-liquid mass ratio 1:120, and leaching at 85° C. for 5 minutes. After leaching, filter to obtain filter residue and filtrate respectively. After determination, the leaching rate of alumina in the filtrate is 80%, and the leaching rates of other components such as silicon dioxide and iron oxide are all zero.
[0046] Put the s...
Embodiment 3
[0053] (1) Mix the crushed bauxite with solid sodium carbonate at a ratio of 1:2.3 and grind it into a 150-mesh mixed material.
[0054] (2) Calcining the mixed material obtained in step (1) at a temperature of 720° C. for 50 minutes to obtain calcined clinker. The roasted clinker is divided into several equal parts with the same quality for later use; during roasting, the roasting equipment is connected to the gas output pipe and connected to the carbon separation tank, and the recovered carbon dioxide gas is directly used for carbon separation.
[0055] (3) Add appropriate amount of water to the first batch of roasted clinker, and make the solid-liquid mass ratio 1:15, and leaching for 40 minutes under the temperature condition of 20°C. After leaching, filter to obtain filter residue and filtrate respectively. After determination, the leaching rate of alumina in the filtrate was 79%, and the leaching rates of other components such as silicon dioxide and iron oxide were all ...
PUM
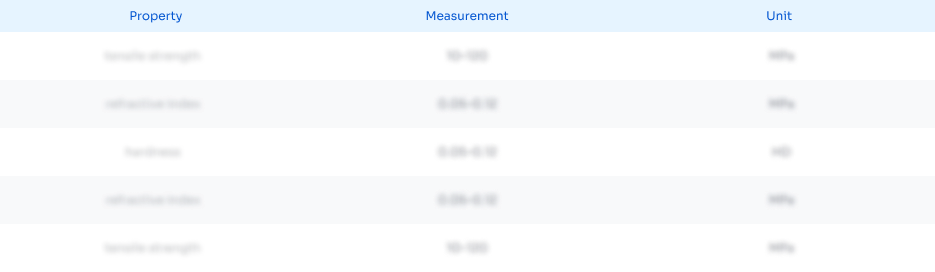
Abstract
Description
Claims
Application Information

- Generate Ideas
- Intellectual Property
- Life Sciences
- Materials
- Tech Scout
- Unparalleled Data Quality
- Higher Quality Content
- 60% Fewer Hallucinations
Browse by: Latest US Patents, China's latest patents, Technical Efficacy Thesaurus, Application Domain, Technology Topic, Popular Technical Reports.
© 2025 PatSnap. All rights reserved.Legal|Privacy policy|Modern Slavery Act Transparency Statement|Sitemap|About US| Contact US: help@patsnap.com