Processing process of cold oil pipe
A processing technology and oil pipe technology, applied in the field of cold oil pipe processing technology, can solve the problems of high material cost, poor heat dissipation efficiency, complicated manufacturing process, etc., and achieve the effect of low material cost, low manufacturing cost and easy implementation
- Summary
- Abstract
- Description
- Claims
- Application Information
AI Technical Summary
Problems solved by technology
Method used
Image
Examples
Embodiment Construction
[0026] Such as Figure 1 to Figure 4 As shown, a kind of cold oil pipe processing technology of the present invention is composed of a circular hollow inner and outer pipe 21, 22 and an oil cooling pipe 20 composed of a cooling fin 23 interposed therebetween. The inner and outer pipes 21, 22 It is an aluminum tube formed by a cutting punching machine, and the two upper ends of the outer tube 22 are oppositely provided with through holes 221. The heat sink 23 is formed by processing an aluminum coil into a number of heat dissipation holes 231 forming a vortex surface. Improve heat dissipation, and set two screw seats 24 that match the through holes 221 at both ends of the outer tube 22. The two screw seats 24 are made of aluminum rods that are processed by a lathe to form a shape, and a concave shape is provided at the bottom of the screw seat 24 The welded portion 241 of the welding part and the assembly end 242 protruding from a hollow external thread, and an end cap 25 with ...
PUM
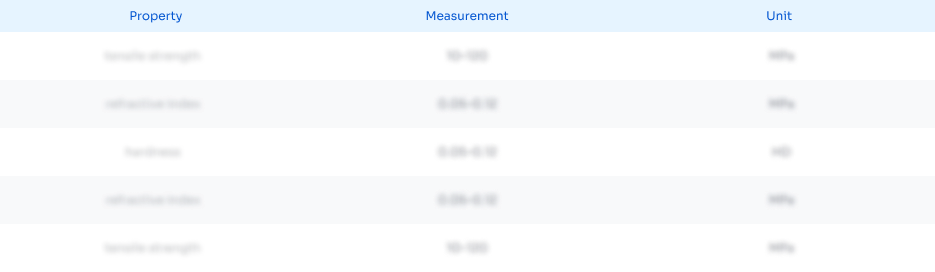
Abstract
Description
Claims
Application Information

- R&D
- Intellectual Property
- Life Sciences
- Materials
- Tech Scout
- Unparalleled Data Quality
- Higher Quality Content
- 60% Fewer Hallucinations
Browse by: Latest US Patents, China's latest patents, Technical Efficacy Thesaurus, Application Domain, Technology Topic, Popular Technical Reports.
© 2025 PatSnap. All rights reserved.Legal|Privacy policy|Modern Slavery Act Transparency Statement|Sitemap|About US| Contact US: help@patsnap.com