Method for separating and extracting uranium and thorium from superior molten slag
A technology for dissolving slag and solution, applied in the field of separation and enrichment of uranium and thorium, can solve the problems of complicated separation process, pollution of equipment, increased load of evaporation and concentration, etc., and achieves cheap and easy-to-obtain raw materials, high product quality, and reduced processing capacity. Effect
- Summary
- Abstract
- Description
- Claims
- Application Information
AI Technical Summary
Problems solved by technology
Method used
Image
Examples
Embodiment 1
[0037] Add 1000g of the excellent melting waste residue and 2000g of water into the reactor, add 50g of sodium hydroxide while stirring, pass carbon dioxide after the addition, control the operating temperature to 80°C, and the pH value to 10, stir for 8 hours and then let it stand for 8 hours , release the supernatant liquid into the reactor, put the solid phase slag in the acid leaching tank; pass carbon dioxide into the clear liquid to make the pH value of the clear liquid slightly lower than 6.5, then add disodium hydrogen phosphate, stir for one hour and let it stand After 4 hours, filter to obtain a high-purity yellow uranyl phosphate product; add 1500g of water to the acid leaching tank of the solid phase slag, then stir and add 250g of sulfuric acid, control the temperature at 100°C, react for 4 hours, and then add 1000g The water was stirred for a few minutes and then left to stand for 10 hours to release the acid leaching solution, add sodium hydroxide to the leaching...
Embodiment 2
[0039]Add 1000g of the excellent soluble waste residue and 2000g of water into the reactor, add 50g of sodium carbonate while stirring, pass carbon dioxide after the addition, control the operating temperature at 80°C, and the pH value is 8.5, stir for 8 hours and then let it stand for 8 hours. Release the supernatant liquid into the reactor, put the solid phase slag in the acid leaching tank; pass carbon dioxide into the clear liquid to make the pH value of the clear liquid slightly lower than 6.5, then add trisodium phosphate, stir for one hour and then let stand for 4 hours , filtered to obtain high-purity yellow uranyl phosphate product; add 1500g of water to the solid-phase slag acid leaching tank, then stir and add 300g of sulfuric acid, control the temperature at 95 ° C, react for 4 hours, then add 1000g of water After stirring for a few minutes, let it stand for 6 hours, release the acid leaching solution, add sodium hydroxide to the leaching solution, control the pH va...
Embodiment 3
[0041] Add 1000g of the excellent soluble waste residue and 2000g of water into the reactor, add 25g of sodium hydroxide and 30g of sodium carbonate while stirring, pass carbon dioxide after the addition, control the operating temperature to 80°C, and the pH value to 9, after stirring for 8 hours Stand still for 8 hours, release the supernatant liquid into the reactor, and place the solid phase slag in the acid leaching tank; pass carbon dioxide into the clear liquid to make the pH value of the clear liquid slightly lower than 6.5, then add disodium hydrogen phosphate, and stir for a while Stand still for 4 hours after 1 hour, filter to obtain high-purity yellow uranyl phosphate product; add 1500g of water to the acid leaching tank of solid phase slag, then stir and add 250g of sulfuric acid, the temperature is controlled at 110 ° C, and react for 4 hours , then add 1000g of water and stir for a few minutes, then let it stand for 8 hours, release the acid leaching solution, add...
PUM
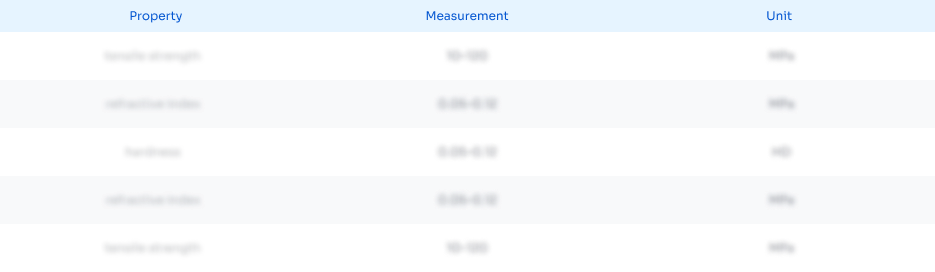
Abstract
Description
Claims
Application Information

- Generate Ideas
- Intellectual Property
- Life Sciences
- Materials
- Tech Scout
- Unparalleled Data Quality
- Higher Quality Content
- 60% Fewer Hallucinations
Browse by: Latest US Patents, China's latest patents, Technical Efficacy Thesaurus, Application Domain, Technology Topic, Popular Technical Reports.
© 2025 PatSnap. All rights reserved.Legal|Privacy policy|Modern Slavery Act Transparency Statement|Sitemap|About US| Contact US: help@patsnap.com