Heat-resistant phenolic resin and application thereof in production of super-hard material resin mold
A phenolic resin, heat-resistant technology, applied in the field of 4,4-biphenol modified phenolic resin, can solve the problems of affecting the grinding efficiency and grinding ratio of abrasive tools, the decrease of cohesive force, and the shedding of abrasives, etc., to achieve good resistance Heat resistance, high softening point, good heat resistance and stability
- Summary
- Abstract
- Description
- Claims
- Application Information
AI Technical Summary
Problems solved by technology
Method used
Image
Examples
Embodiment 1
[0019] Add 0.05mol (9.3g) of 4,4-biphenol, 0.86mol (70g) of 36.7% formaldehyde solution and 10mL of 20% HCl into the three-necked flask, start the stirrer, control the pH value at 1.9-2.3, and slowly raise the temperature to 80 ℃, dissolve while stirring within 30min, after the biphenol is completely dissolved, cool down to 50℃, add 0.95mol (89.3g) phenol, slowly raise the temperature to 90℃, react for 30min, then raise the temperature to 95℃ and keep boiling for about 30min, Then slowly add the remaining 20mL of 20% HCl dropwise within 30 minutes, control the reaction temperature at 105-107°C, boil and stir until the end point, vacuumize after the end point, the final temperature reaches 145°C, stop heating, quickly discharge, and cool to room temperature, Crush and sieve to get 5% heat-resistant phenolic resin powder (4,4-biphenol modified phenolic resin powder).
Embodiment 2
[0021] Add 0.2mol (39.2g) of 4,4-biphenol, 0.86mol (70g) of 36.7% formaldehyde solution and 2g of oxalic acid HCl into the three-necked flask, start the stirrer, control the pH value at 1.9-2.3, and slowly raise the temperature to 80 ℃, dissolve while stirring within 30 minutes, after the biphenol is completely dissolved, cool down to 50 ℃, add 0.80mol (75.3g) phenol, slowly raise the temperature to 90 ℃, after 30 minutes of reaction, raise the temperature to 95 ℃ and keep boiling for about 30 minutes, Then slowly add the remaining 3g of oxalic acid within 30 minutes, control the reaction temperature at 105-107°C, boil and stir until the end point, vacuumize after the end point, stop heating, discharge the material quickly, cool to room temperature, and pulverize, Sieve to get 20% heat-resistant phenolic resin powder (4,4-biphenol modified phenolic resin powder).
Embodiment 3
[0023] Add 0.05mol (9.3g) of 4,4-biphenol, 1.2mol (114.4g) of 36.7% formaldehyde solution and 10mL of 20% NaOH aqueous solution into the three-necked flask, start the stirrer, control the pH value at about 13, and slowly rise to 60°C, react for 30 minutes and then raise the temperature to 70°C. After the biphenol is completely dissolved, add 0.95mol (89.3g) phenol, react at 70°C for 30 minutes, gradually raise the temperature to 80°C and keep it for 30 minutes, then raise the temperature to 90°C and keep it for 1 hour. Until the end point, lower the temperature to below 60°C and vacuum dehydrate. After the dehydration is complete in about 30 minutes, a heat-resistant phenolic resin solution with a content of 5% (4,4-biphenol modified phenolic resin solution) is obtained.
PUM
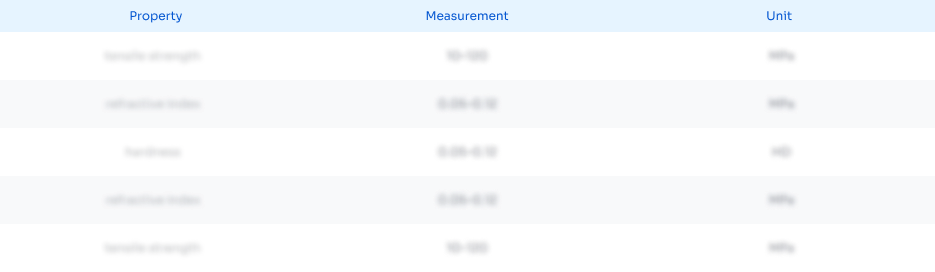
Abstract
Description
Claims
Application Information

- R&D
- Intellectual Property
- Life Sciences
- Materials
- Tech Scout
- Unparalleled Data Quality
- Higher Quality Content
- 60% Fewer Hallucinations
Browse by: Latest US Patents, China's latest patents, Technical Efficacy Thesaurus, Application Domain, Technology Topic, Popular Technical Reports.
© 2025 PatSnap. All rights reserved.Legal|Privacy policy|Modern Slavery Act Transparency Statement|Sitemap|About US| Contact US: help@patsnap.com