Pre-melted refining slag
A refining slag and pre-melting technology, which is applied in the field of iron and steel smelting, can solve the problems of unfavorable refining slag desulfurization and volume expansion, and achieve the effects of small erosion, fast slagging speed and large capacity
- Summary
- Abstract
- Description
- Claims
- Application Information
AI Technical Summary
Problems solved by technology
Method used
Image
Examples
Embodiment 1
[0015] CaO92% of active lime is selected, and the rest are impurities;
[0016] In the high alumina bauxite composition, Al 2 o 3 88%, Fe 2 o 3 1.5%, SiO 2 5%, the others are impurities;
[0017] In the composition of magnesia, MgO93%, CaO1.6%, SiO 2 3.5%, caustic soda 0.3%, others are impurities;
[0018] Among the borax ingredients, B 2 o 3 68%, Na 2 O30%, Na 2 CO 3 0.5%, Na 2 SO 4 0.4%, NaCl0.1%, others are impurities;
[0019] The above-mentioned raw materials are as follows according to the weight ratio: active lime 68, high alumina bauxite 23, borax 1, magnesia 2, through crushing, batching, mixing, pre-melting and other processes to synthesize refining slag.
Embodiment 2
[0021] Among the ingredients of active lime, CaO93%, the others are impurities;
[0022] In the high alumina bauxite composition, Al 2 o 3 89%, Fe 2 o 3 1%, SiO 2 4%, the others are impurities;
[0023] Among the magnesia components, MgO95%, CaO1%, SiO 2 2%, caustic soda 0.1%, others are impurities;
[0024] Among the borax ingredients, B 2 o 3 69%, Na 2 O29%, Na 2 CO 3 0.3%, Na 2 SO 4 0.2%, NaCl0.05%, others are impurities;
[0025] The above raw materials are prepared according to weight ratio as follows: active lime 60, high alumina bauxite 30, borax 5, magnesia 7, through crushing, batching, mixing, pre-melting and other processes to synthesize refining slag.
Embodiment 3
[0027] Among the ingredients of active lime, CaO95%, the others are impurities;
[0028] In the high alumina bauxite composition, Al 2 o 3 90%, Fe 2 o 3 0.5%, SiO 2 3%, others are impurities;
[0029] In the composition of magnesia, MgO95%, CaO0.5%, SiO 2 2%, the others are impurities;
[0030] Among the borax ingredients, B 2 o 3 69%, Na 2 O30%, Na 2 CO 3 0.5%, Na 2 SO 4 0.4%, NaCl0.1%;
[0031] The above-mentioned raw materials are compared by weight as follows: active lime 54, high alumina bauxite 35, borax 6, magnesia 4, through crushing, batching, mixing, pre-melting and other processes to synthesize refining slag.
[0032] In addition, the refining slag can be prepared separately according to different weight ratios of the components, and the desulfurization kinetic experiment between the RH desulfurization refining slag and molten steel can be carried out by using a thyristor intermediate frequency induction furnace. Table 1 lists the test formulations, w...
PUM
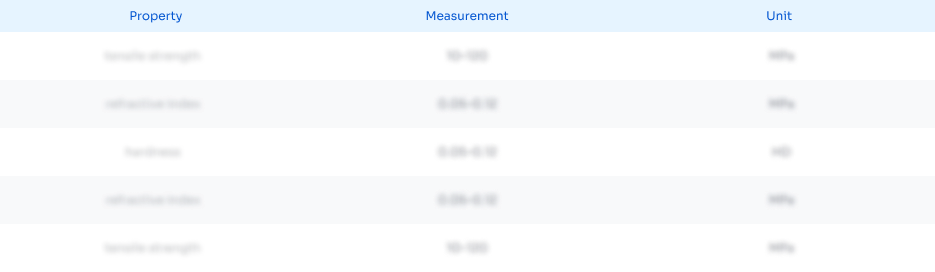
Abstract
Description
Claims
Application Information

- R&D
- Intellectual Property
- Life Sciences
- Materials
- Tech Scout
- Unparalleled Data Quality
- Higher Quality Content
- 60% Fewer Hallucinations
Browse by: Latest US Patents, China's latest patents, Technical Efficacy Thesaurus, Application Domain, Technology Topic, Popular Technical Reports.
© 2025 PatSnap. All rights reserved.Legal|Privacy policy|Modern Slavery Act Transparency Statement|Sitemap|About US| Contact US: help@patsnap.com