Corrosion-resistance optimizing treatment process for Cr-Ni type stainless steel and corrosion-resistant plate
A technology of corrosion resistance and treatment process, which is applied in the optimization of corrosion resistance of austenitic stainless steel components, and in the field of metallurgy, can solve the problems of long annealing cycle, coarse grain structure, discount of GBCD optimization effect, etc., to improve intergranular corrosion The effects of resistance, grain shedding reduction, and simplified optimization process
- Summary
- Abstract
- Description
- Claims
- Application Information
AI Technical Summary
Problems solved by technology
Method used
Image
Examples
Embodiment 1
[0035] The hot-rolled 316 austenitic stainless steel plate is optimized. The alloy composition is (mass ratio, wt%): 0.013C, 0.69Si, 0.96Mn, 0.31P, 0.001S, 17.4Cr, 12.45Ni, 2.0Mo, The initial sample grain size was 20 μm.
[0036] In the first step, using a Φ180 two-roller test rolling mill, the hot-rolled plate is subjected to cold-rolling deformation with a reduction of 4%.
[0037] In the second step, the cold-rolled alloy plate is annealed. The temperature rise rate of the vacuum annealing furnace is 20-30°C / min, and it is kept at 925°C for 80-90 minutes, then water-cooled to obtain an incomplete recrystallized structure; Keep warm at ℃ for 10-15 minutes (heating rate is 20-30 ℃ / min), water-cooled; repeat the process of the previous step 2 times.
[0038] The corrosion-resistant Cr-Ni stainless steel plate obtained after optimization treatment was tested by EBSD, and its grain boundary ratio and reconstruction diagram are shown in Table 1 and Figure 4 shown. The proport...
Embodiment 2
[0042] The 304 austenitic stainless steel plate that has been solid-solved at 1050°C for 30 minutes is optimized. S, 0.07Mo, initial sample with a grain size of 15 μm.
[0043] In the first step, the stainless steel plate is first subjected to cold rolling deformation with a reduction of 5%.
[0044] In the second step, the cold-rolled alloy plate is kept at 920°C for 70-80 minutes (the heating rate is 20-30°C / min), water-cooled to obtain an incomplete recrystallized structure; and then kept at 1060°C for 10-15 minutes ( The heating rate is 20-30°C / min), water cooling; repeat the process of the previous step once.
[0045] The corrosion-resistant Cr-Ni stainless steel plate obtained after optimization treatment was tested by EBSD, and its grain boundary ratio and reconstruction diagram are shown in Table 2 and Figure 5 shown. The proportion of the optimized special grain boundary is 79.6%, and it is distributed on the general high-angle grain boundary, which effectively in...
Embodiment 3
[0049] The 304 austenitic stainless steel plate aged at 650°C for 2 hours after solid solution was optimized. P, 0.0053S, 0.07Mo, the grain size is 20μm, and carbides are discontinuously precipitated along the grain boundaries.
[0050] In the first step, the alloy plate is subjected to cold rolling deformation with a reduction of 3%.
[0051] In the second step, the cold-rolled alloy plate is kept at 900°C for 70-80min (heating rate is 20-30°C / min), and water-cooled; then it is kept at 1050°C for 10-15min (heating rate is 20-30°C / min). min), water cooling; repeat the previous step process 3 times.
[0052] The corrosion-resistant Cr-Ni stainless steel plate obtained after optimization treatment was tested by EBSD, and its grain boundary ratio and reconstruction diagram are shown in Table 3 and Image 6 shown. The proportion of the optimized special grain boundary is 86.6%, and it is distributed on the general high-angle grain boundary, which effectively interrupts the netw...
PUM
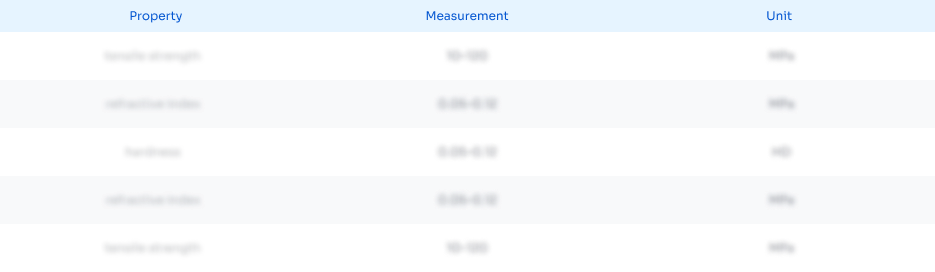
Abstract
Description
Claims
Application Information

- Generate Ideas
- Intellectual Property
- Life Sciences
- Materials
- Tech Scout
- Unparalleled Data Quality
- Higher Quality Content
- 60% Fewer Hallucinations
Browse by: Latest US Patents, China's latest patents, Technical Efficacy Thesaurus, Application Domain, Technology Topic, Popular Technical Reports.
© 2025 PatSnap. All rights reserved.Legal|Privacy policy|Modern Slavery Act Transparency Statement|Sitemap|About US| Contact US: help@patsnap.com