Stacked secondary battery and method of manufacturing the same
A secondary battery, laminated technology, applied in secondary battery manufacturing, secondary battery, electrode manufacturing, etc., can solve problems such as difficult and reliable stamping, and achieve the effects of reduced shedding, high adhesion strength, and excellent charge and discharge characteristics
- Summary
- Abstract
- Description
- Claims
- Application Information
AI Technical Summary
Problems solved by technology
Method used
Image
Examples
Embodiment 1
[0049] Prepare 63 parts by mass of lithium manganese composite oxide with a number average particle diameter of 15 μm, 4.2 parts by mass of acetylene black with a number average particle diameter of 7 μm, 2.8 parts by mass of polyvinylidene fluoride, and 30 parts by mass of N-methyl-2-pyrrolidone Partially constituted slurry.
[0050] Make the uncoated length of 20 mm over the entire width of the aluminum foil with a thickness of 20 μm and a width of 150 mm for the current collector, apply intermittently with a coating length of 130 mm, dry and press to form a positive electrode with a thickness of 180 μm active material layer.
[0051] Electrode lead-out terminals were formed on the uncoated part with a width of 13 mm and a length of 17 mm, and were irradiated under the irradiation conditions of a spot diameter of 12 μm, a laser output of 20 W, and a laser repetition frequency of 20 kHz to 100 kHz using a YAG laser with a laser wavelength of 1060 nm. In addition, cutting was...
Embodiment 2
[0054] Except that the relative moving speed of the laser beam and the positive electrode active material layer is 40 mm / sec, the same section of the positive electrode obtained by cutting in the same manner as in Example 1 was photographed, and the Figure 4 The result is shown.
Embodiment 3
[0060] Preparation is composed of 49 parts by mass of graphite with a number average particle diameter of 10 μm, 0.5 parts by mass of acetylene black with a number average particle diameter of 7 μm, 3.5 parts by mass of polyvinylidene fluoride, and 47 parts by mass of N-methyl-2-pyrrolidone slurry.
[0061] Make the uncoated length of 20 mm over the entire width of the copper foil with a thickness of 10 μm and a width of 150 mm for the current collector, apply intermittently with a coating length of 130 mm, dry and press to form a 112 μm thick copper foil. Negative electrode active material layer.
[0062] In the uncoated part, an electrode lead-out terminal is formed with a width of 13mm and a length of 15mm. Using a YAG laser with a laser wavelength of 1060nm, the spot diameter is 12μm, the laser output is 20W, and the relative movement speed of the laser and the negative electrode active material layer is 20mm. Cutting was performed by irradiating laser twice at a rate of ...
PUM
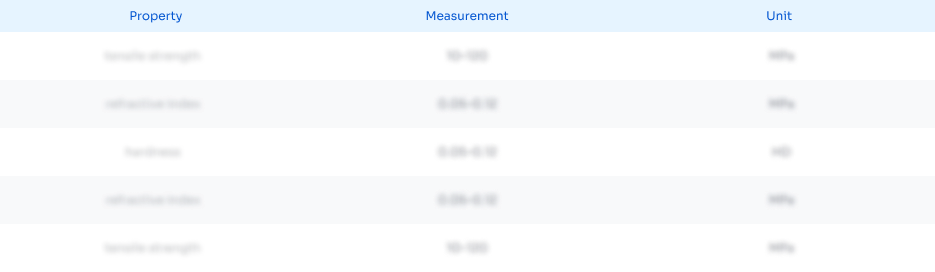
Abstract
Description
Claims
Application Information

- R&D
- Intellectual Property
- Life Sciences
- Materials
- Tech Scout
- Unparalleled Data Quality
- Higher Quality Content
- 60% Fewer Hallucinations
Browse by: Latest US Patents, China's latest patents, Technical Efficacy Thesaurus, Application Domain, Technology Topic, Popular Technical Reports.
© 2025 PatSnap. All rights reserved.Legal|Privacy policy|Modern Slavery Act Transparency Statement|Sitemap|About US| Contact US: help@patsnap.com