Work starting method for hydrogenation process
A process and technology for starting oil, applied in refining to remove heteroatoms, etc., can solve the problems of affecting the timely start of hydrogenation units, increase processing costs, and take a long time to achieve shortened production cycle, efficient utilization, and reduced usage. Effect
- Summary
- Abstract
- Description
- Claims
- Application Information
AI Technical Summary
Problems solved by technology
Method used
Examples
Embodiment 1
[0047] 50 g of the catalyst 100 g is impregnated in 10 g of organic solvent (organic solvent is coking kerosene fraction), the ratio of carbon number 9 to 12 in the organic solvent is not less than 50%, and the immersion time is 1 hour. Elemental sulfur 10g and 5g (NH 4 ) 2 S mixed. The impregnated catalyst was mixed with a vulcanizing agent, treated at 180° C. for 3 hours, and cooled naturally to obtain a pre-sulfided catalyst A. Mix the obtained presulfurized catalyst A with the remaining 50g of the unpresulfurized catalyst evenly, put it into a small reactor, and make it airtight, adjust the hydrogen partial pressure to 6.0MPa and start to raise the temperature at 20°C / h, and start to rise to 80°C Add vulcanized oil from the bottom of the reactor to carry out closed-circuit circulation of the device. The vulcanized oil is straight-run kerosene, and the conditions are hydrogen-oil volume ratio 350:1, volume space velocity 2.0h -1 . When the temperature rises to 270°C, ke...
Embodiment 2
[0051] 70 g of the catalyst 100 g was immersed in 10 g of organic solvent (the organic solvent was a mixture of coker kerosene fraction and cottonseed oil at a volume ratio of 2:1), and the soaking time was 1 hour. Elemental sulfur 10g and 5g (NH 4 ) 2 S mixed. The impregnated catalyst was mixed with a vulcanizing agent, treated at 150° C. for 5 hours, and cooled naturally to obtain a pre-sulfided catalyst A. The obtained vulcanizing agent A and the remaining non-presulfurized catalyst are respectively loaded into a small reactor, and the presulfurized catalyst is loaded in the lower part of the remaining oxidation state catalyst. The airtightness is qualified, the hydrogen partial pressure is adjusted to 6.0MPa, and the temperature is raised at 20°C / h. When it rises to 80°C, sulfurized oil is added from the bottom of the reactor to perform closed-circuit circulation of the device. The sulfurized oil is straight-run kerosene, and the condition is the volume ratio of hydrogen...
Embodiment 3
[0053] 30 g of the catalyst 100 g was immersed in 10 g of organic solvent (the organic solvent was a fraction of coked diesel oil), and the immersion time was 1 hour. Elemental sulfur 12g and 5g (NH 4 ) 2 S mixed. The impregnated catalyst was mixed with a vulcanizing agent, treated at 200° C. for 2 hours, and cooled naturally to obtain a pre-sulfided catalyst A. The obtained presulfided catalyst A and the oxidation state catalyst without presulfurization treatment are loaded into small reactors respectively, and the loading is to load the presulfided catalyst at the lower part of the oxidation state catalyst. The airtightness is qualified, the hydrogen partial pressure is adjusted to 6.0MPa, and the temperature is raised at 20°C / h. When it rises to 80°C, sulfurized oil is added from the bottom of the reactor to perform closed-circuit circulation of the device. The sulfurized oil is straight-run kerosene, and the condition is the volume ratio of hydrogen to oil. 350:1, volum...
PUM
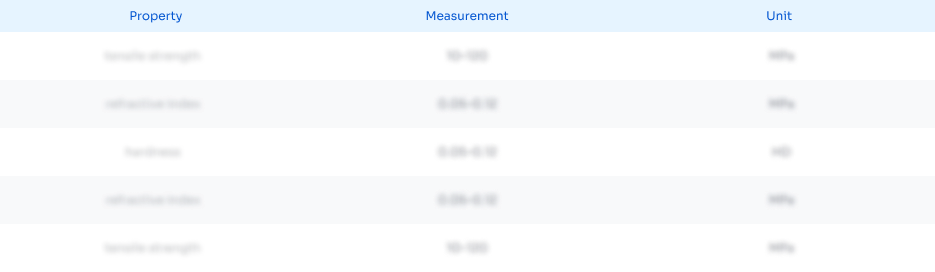
Abstract
Description
Claims
Application Information

- R&D
- Intellectual Property
- Life Sciences
- Materials
- Tech Scout
- Unparalleled Data Quality
- Higher Quality Content
- 60% Fewer Hallucinations
Browse by: Latest US Patents, China's latest patents, Technical Efficacy Thesaurus, Application Domain, Technology Topic, Popular Technical Reports.
© 2025 PatSnap. All rights reserved.Legal|Privacy policy|Modern Slavery Act Transparency Statement|Sitemap|About US| Contact US: help@patsnap.com