Method for regulating intermetallic compound for dissimilar material overlap joint through laser-arc double-sided welding
A technology of intermetallic compounds and lap joints, which is applied in welding equipment, metal processing equipment, manufacturing tools, etc., can solve the problems of poor mechanical properties of joints and difficult control of the thickness of intermetallic compounds, etc., so as to improve the weld structure and excellent Joint performance, effect of delaying cooling time
- Summary
- Abstract
- Description
- Claims
- Application Information
AI Technical Summary
Problems solved by technology
Method used
Image
Examples
specific Embodiment approach 1
[0009] Embodiment 1: In this embodiment, the laser-arc double-sided welding method for regulating the intermetallic compound of the lap joints of dissimilar materials is as follows: pre-set solder between the lap joints of dissimilar materials, and then place the laser beam and the arc on the lap joints respectively. The two sides of the joint are symmetrically heated and welded at the same time, among which the laser beam deep penetration welding on the low melting point material side, and the arc solder brazing welding on the high melting point material side.
specific Embodiment approach 2
[0010] Embodiment 2: This embodiment is different from Embodiment 1 in that: the brazing filler metal is welding wire or an intermediate layer. Other steps and parameters are the same as in the first embodiment.
specific Embodiment approach 3
[0011] Specific embodiment three: the difference between this embodiment and specific embodiment one or two is: the type of laser beam is CO 2 Gas laser beam, YAG solid-state laser beam, semiconductor laser beam or fiber laser beam. Other steps and parameters are the same as those in Embodiment 1 or Embodiment 2.
PUM
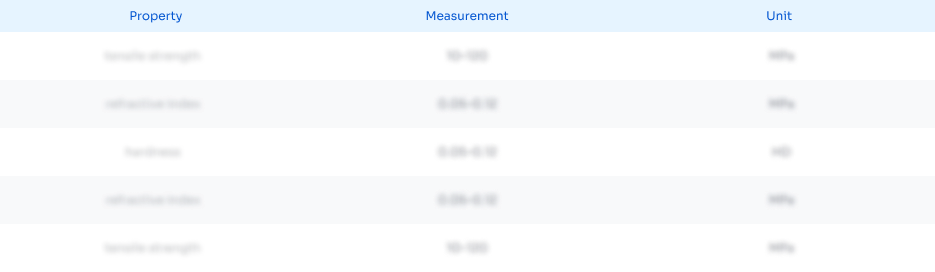
Abstract
Description
Claims
Application Information

- R&D
- Intellectual Property
- Life Sciences
- Materials
- Tech Scout
- Unparalleled Data Quality
- Higher Quality Content
- 60% Fewer Hallucinations
Browse by: Latest US Patents, China's latest patents, Technical Efficacy Thesaurus, Application Domain, Technology Topic, Popular Technical Reports.
© 2025 PatSnap. All rights reserved.Legal|Privacy policy|Modern Slavery Act Transparency Statement|Sitemap|About US| Contact US: help@patsnap.com