Explosion welding forming device for titaniumtim and ordinary low-alloy steel composite head
A low-alloy steel and composite head technology, which is applied in the field of explosive welding forming devices, can solve problems such as contamination, difficulty in realization, and failure to form normally, and achieve excellent performance, good joint performance, and compact structure.
- Summary
- Abstract
- Description
- Claims
- Application Information
AI Technical Summary
Problems solved by technology
Method used
Image
Examples
Embodiment Construction
[0016] The present invention will be described in detail below in conjunction with the accompanying drawings and specific embodiments.
[0017] The explosive welding forming device of titanium material and common low-alloy steel composite head of the present invention, see attached figure 1 , including ordinary low-alloy steel head base layer 2, titanium head cover layer 3, buffer layer 4 and special-shaped explosive bag 6, ordinary low-alloy steel head base layer 2 is set on the sand base layer 1, titanium head cover layer 3 It is arranged on the base layer 2 of ordinary low-alloy steel head and has a certain gap with the base layer 2 of ordinary low-alloy steel head. Support plate support plate 8 is welded with support plate 9, as figure 2 As shown, the inner side of the support plate support plate 8 is provided with a groove, and one end of the support plate 9 welded on the support plate support plate 8 is flat, and the other end is arc-shaped, and one end of the arc shap...
PUM
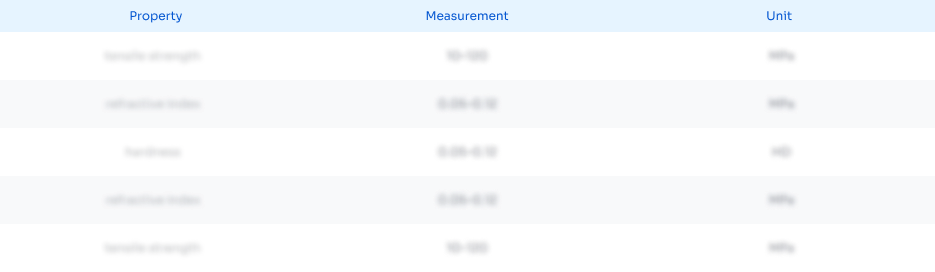
Abstract
Description
Claims
Application Information

- R&D Engineer
- R&D Manager
- IP Professional
- Industry Leading Data Capabilities
- Powerful AI technology
- Patent DNA Extraction
Browse by: Latest US Patents, China's latest patents, Technical Efficacy Thesaurus, Application Domain, Technology Topic, Popular Technical Reports.
© 2024 PatSnap. All rights reserved.Legal|Privacy policy|Modern Slavery Act Transparency Statement|Sitemap|About US| Contact US: help@patsnap.com