Composite flexible insulator and manufacturing method and application thereof
A manufacturing method and technology of insulators, which are applied in the field of insulator technology and composite materials, can solve problems such as poor bending resistance and torsion resistance, and achieve the effects of environmental aging resistance, good electrical insulation, and soft structure
- Summary
- Abstract
- Description
- Claims
- Application Information
AI Technical Summary
Problems solved by technology
Method used
Image
Examples
example 1
[0028] Use the mixed tow of nylon and basalt fiber with a weight ratio of 1:1, degrease in a mixed solvent of ethanol and ether with a weight ratio of 1:1, dry it at 102°C for 1 hour, and then immerse it in bismaleimide resin. Pull extrusion molding at 200°C, and become a flexible core 101 after curing. Mix 100 parts by mass of a 1:1 compound of silicone rubber and fluorosilicone rubber with 40 to 50 parts by mass of fumed white carbon black at 60 to 100°C for 1 to 3 hours, add 50 to 70 parts by mass of alumina powder and 10 ~20 parts by mass of antimony oxide powder is refined at 100~150°C and vacuum degree of 80~90kPa for 2~3 hours, taken out and re-milled on a two-roll machine for 3 to 4 times, and 1~3 parts by mass of benzoyl peroxide and 1 ~3 parts by mass of UV-9 UV antioxidant, kneaded to become a rubber base material. The flexible core 101 is extruded with the above-mentioned rubber base material in an extruder, and vulcanized at a high temperature in a vulcanization ...
example 2
[0031] The mixed fiber braid of aramid fiber and polyphenylene sulfide fiber in a weight ratio of 2:1 is degreased in a mixed solvent of ethanol and ether in a weight ratio of 1:1, dried at 105°C for 1 hour, and then immersed in fluorosilicone rubber. ~160°C down-draw extrusion molding, and become a flexible core 101 after vulcanization. Mix 100 parts by mass of silicone rubber with 30-40 parts by mass of fumed white carbon black at 50-80°C for 1-3 hours, add 60-80 parts by mass of alumina powder and 10-20 parts by mass of antimony oxide powder at 100-80°C Refining at 130°C and a vacuum of 80-90kPa for 2-3 hours, take it out and re-refining it on a two-roller machine for 3-4 times and add 2-5 parts by mass of cumene peroxide and 1-3 parts by mass of UV-326 ultraviolet antioxidant , and knead evenly to become a rubber compound. Put the flexible core 101 in the mold, add the refined rubber material into the rubber material bin, start the injection molding machine, inject the ru...
example 3
[0034]Aramid fiber tow is degreased in a mixed solvent of ethanol and ether in a weight ratio of 1:2, dried at 105°C for 1 hour, then immersed in silicone resin, drawn down at 90-160°C, and cured to become a flexible core 101. Mix 100 parts by mass of fluorosilicone rubber with 40-50 parts by mass of fumed white carbon black at 80-120°C for 1-3 hours, add 50-90 parts by mass of alumina powder and 10-15 parts by mass of antimony oxide powder at 90 Refining at ~150°C and vacuum degree of 80~90kPa for 2~3 hours, take it out and remelt it on a two-roll machine for 3~4 times, and add 2~3 parts by mass of cumene peroxide and 1~2 parts by mass of UV-9 ultraviolet anti-aging agent, kneaded into a rubber base material. The flexible core 101 is extruded by adding the rubber base material in the extruder, and vulcanized at a high temperature of 120-180° C. in a vulcanization furnace to become the flexible shaft 100 with the outer sheath 102 . The shed 200 is made by molding the rubber ...
PUM
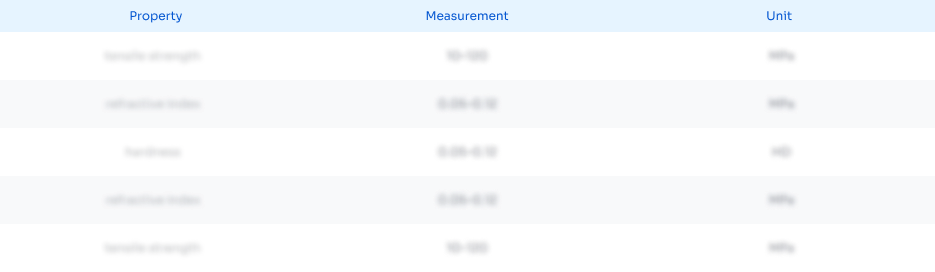
Abstract
Description
Claims
Application Information

- Generate Ideas
- Intellectual Property
- Life Sciences
- Materials
- Tech Scout
- Unparalleled Data Quality
- Higher Quality Content
- 60% Fewer Hallucinations
Browse by: Latest US Patents, China's latest patents, Technical Efficacy Thesaurus, Application Domain, Technology Topic, Popular Technical Reports.
© 2025 PatSnap. All rights reserved.Legal|Privacy policy|Modern Slavery Act Transparency Statement|Sitemap|About US| Contact US: help@patsnap.com