Colloidal forming process method for preparing silicon nitride bonded silicon carbide composite ceramic
A composite ceramic and colloidal molding technology, applied in the field of engineering ceramics, achieves the effects of easy control, simple operation process and reduced production cost
- Summary
- Abstract
- Description
- Claims
- Application Information
AI Technical Summary
Problems solved by technology
Method used
Image
Examples
Embodiment 1
[0031] 1~8wt% concentration agar deionized aqueous solution (relative solid powder 1wt%), 80.5wt% silicon carbide powder, 15wt% silicon powder, 4wt% aluminum oxide, 0.5wt% ferric oxide and 0.1wt% ammonium citrate (relative Add deionized water to solid powder, mix and ball mill for 24 hours to form a uniform slurry; heat and stir in a deionized water bath at 80°C to fully dissolve the agar in the slurry, vacuumize and remove bubbles for 10 minutes, and pour into a beaker This process is assisted by ultrasonic treatment; inject the hot slurry into the cold mold, place it at room temperature, and obtain a cured wet billet after demoulding, dry in the shade for 24 hours, put it in an oven to heat and dry, and get the required Shape and size of the body. figure 1 is the strength of dry bodies containing different concentrations of agar gel.
Embodiment 2
[0033] 9 wt% agar deionized aqueous solution (2 wt% relative to solid powder) was added into deionized water and heated to dissolve at 45°C for use. 77.2wt% silicon carbide powder, 17.5wt% silicon powder, 0.3wt% ferric oxide, 4wt% aluminum oxide, 1wt% yttrium oxide, deionized water and 1wt% ammonium citrate (relative to solid powder) after 12 hours Ball milling, heating and stirring with the prepared agar solution, vacuumize and remove foam to form a uniform slurry; vacuumize and remove foam at 60°C, inject the slurry into molds, cool and solidify for 20 minutes, then demould, dry in the shade, and bake Dry to obtain a green body of the desired shape and size. figure 1 is the strength of dry bodies containing different concentrations of agar gel.
Embodiment 3
[0035] Add the gelatin deionized aqueous solution with a concentration of 3wt-9wt% (3wt% relative to the solid powder) into deionized water and heat to dissolve at 50°C for use. 82.5wt% silicon carbide powder, 15.5wt% silicon powder, 2wt% yttrium oxide, deionized water and 0.5wt% ammonium citrate (relative to solid powder) were ball milled for 12 hours, heated and stirred with the prepared gelatin solution , vacuumize at 40°C to remove foam to form a uniform slurry; inject the slurry into a mold, cool and solidify for 30 minutes, then demould, dry in the shade, and dry to obtain a green body of the desired shape and size. figure 2 is the strength of dry bodies containing different concentrations of gelatin gel.
PUM
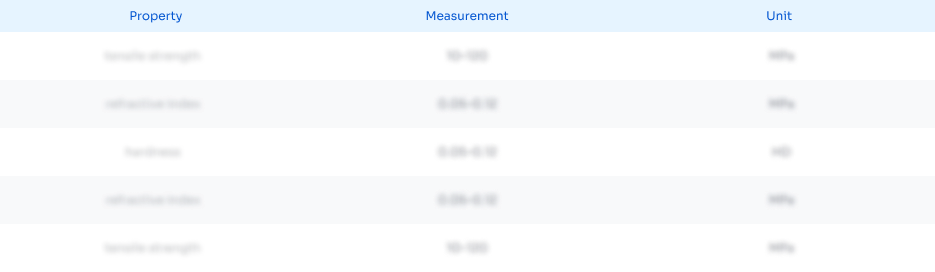
Abstract
Description
Claims
Application Information

- R&D
- Intellectual Property
- Life Sciences
- Materials
- Tech Scout
- Unparalleled Data Quality
- Higher Quality Content
- 60% Fewer Hallucinations
Browse by: Latest US Patents, China's latest patents, Technical Efficacy Thesaurus, Application Domain, Technology Topic, Popular Technical Reports.
© 2025 PatSnap. All rights reserved.Legal|Privacy policy|Modern Slavery Act Transparency Statement|Sitemap|About US| Contact US: help@patsnap.com