Preparation method of low-temperature selective catalytic reduction (SCR) catalyst by removing NOx from flue gas
A SCR catalyst and catalyst technology, applied in chemical instruments and methods, physical/chemical process catalysts, separation methods, etc., can solve the problems of catalyst alkali metal poisoning, dust blockage, high reaction temperature, etc., to improve dispersion and bonding strength, The effect of lowering the operating temperature and increasing the reaction rate
- Summary
- Abstract
- Description
- Claims
- Application Information
AI Technical Summary
Problems solved by technology
Method used
Image
Examples
Embodiment 1
[0033] Dissolve titanium sulfate in water, add 30% ammonia water drop by drop to get white Ti(OH) 4 Precipitation, after the precipitation is complete, filter and wash to remove sulfate ions. Dissolve the white precipitate completely with nitric acid with a concentration of 20%, add manganese nitrate and cerium nitrate to the solution, and then gradually add ammonia water with a concentration of 30% to obtain the precipitate, filter, wash, dry at 120°C, and then Calcined at 450°C for 6h to obtain Mn-Ce / TiO 2 catalyst. Wherein the molar ratio is: Mn:Ce:Ti=0.4:0.05:1.
[0034] Prepared Mn-Ce / TiO 2 Catalyst XRD see figure 1 , A in the figure represents anatase, and B represents brookite. It can be seen from the peak characteristics of XRD that only two peaks of anatase and brookite appear, and no peaks related to Mn and Ce appear, that is, no crystal phase containing Mn is detected. It shows that the dispersion of Mn and Ce oxides in the catalyst is better, so that the cata...
Embodiment 2
[0037] Dissolve titanyl sulfate in water, and add ammonia water with a concentration of 30% dropwise to obtain white Ti(OH) 4 Precipitation, after the precipitation is complete, filter and wash to remove sulfate ions. Dissolve the white precipitate completely with nitric acid with a concentration of 20%, add manganese nitrate and cerium nitrate to the solution, and then gradually add ammonia water with a concentration of 30% to obtain a precipitate, filter, wash, dry at 120°C, and then Calcined at 450°C for 6h to obtain Mn-Ce / TiO 2 catalyst. Wherein the molar ratio is: Mn:Ce:Ti=0.3:0.1:1.
[0038] The catalyst is used for SCR denitrification of flue gas, flue gas GHSV (gas space velocity per hour) = 30000h -1 , O 2 Volume concentration 3%, denitration agent NH 3 Press NO:NH 3 =1 (molar ratio) is added, and when the reaction temperature is 100° C., the catalytic efficiency is about 85%. Add 150ppm SO in the flue gas 2 and 8% H 2 After O, the catalytic efficiency was 85...
Embodiment 3
[0040] Dissolve titanium tetrachloride in water (ice-water bath), add 10% ammonia water drop by drop to obtain white Ti(OH) 4 Precipitation, after the precipitation is complete, filter and wash to remove chloride ions. Dissolve the white precipitate completely with 20% nitric acid, add manganese nitrate and cerium nitrate to the solution, and then gradually drop in 10% ammonia water to obtain the precipitate, filter, wash, dry at 120°C, and then Calcined at 500°C for 6h to obtain Mn-Ce / TiO 2 catalyst. Wherein the molar ratio is: Mn:Ce:Ti=0.4:0.05:1.
[0041] The catalyst is used for SCR denitrification of flue gas, flue gas GHSV (gas space velocity per hour) = 30000h -1 , O 2 Volume concentration 3%, denitration agent NH 3 Press NO:NH 3 =1 (molar ratio) is added, and when the reaction temperature is 120° C., the catalytic efficiency is about 94%. Add 150ppm SO in the flue gas 2 and 8% H 2 After O, the catalytic efficiency was 88%.
PUM
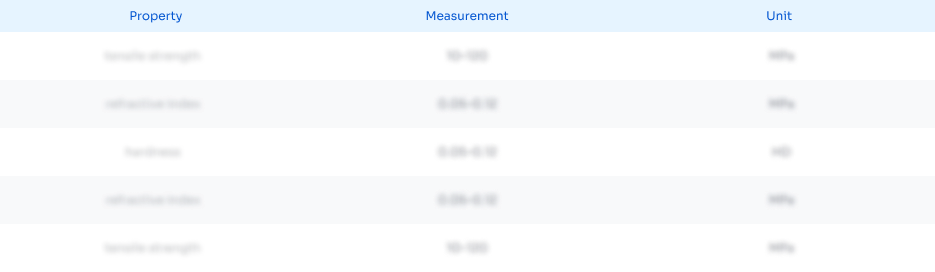
Abstract
Description
Claims
Application Information

- R&D
- Intellectual Property
- Life Sciences
- Materials
- Tech Scout
- Unparalleled Data Quality
- Higher Quality Content
- 60% Fewer Hallucinations
Browse by: Latest US Patents, China's latest patents, Technical Efficacy Thesaurus, Application Domain, Technology Topic, Popular Technical Reports.
© 2025 PatSnap. All rights reserved.Legal|Privacy policy|Modern Slavery Act Transparency Statement|Sitemap|About US| Contact US: help@patsnap.com