Clean method for preparing low-sulfur chromium oxide green
A technology of chromium oxide green and chromium oxide sulfur, applied in the directions of chromium trioxide, chromium oxide/hydrate, etc., can solve the problems of high energy consumption, high reaction temperature, complex reaction equipment, etc., and achieve the effect of zero emission
- Summary
- Abstract
- Description
- Claims
- Application Information
AI Technical Summary
Problems solved by technology
Method used
Examples
Embodiment 1
[0016] The reduction of 1000g of sodium chromate is carried out in a box-type reduction furnace, using hydrogen as the reducing gas, the reduction temperature is 450°C, the reduction time is 2h, and the hydrogen flow rate during the reduction process is 0.6L / min.
[0017] After the reduction product is cooled, it is washed with cold water. During the washing process, the liquid-solid volume ratio is 1.00-1.05, and the washing temperature is 20°C. Wash, filter, and dry to obtain an intermediate product, and the filtered liquid is a chromium-free NaOH solution for recycling.
[0018] The intermediate product was dry-milled in a ball mill according to a ball-to-material ratio of 20:1, a rotational speed of 300 rpm / min, and a ball milling time of 30 minutes to obtain a ground product. The lining material of the ball mill is ZrO 2 , the ball is ZrO 2 ball.
[0019] The ground product was subjected to hydrothermal leaching in an autoclave, the leaching temperature was 200° C., th...
Embodiment 2
[0023] The reduction of 1000g of sodium chromate is carried out in a box-type reduction furnace, using hydrogen as the reducing gas, the reduction temperature is 500°C, the reduction time is 2h, and the hydrogen flow rate during the reduction process is 0.6L / min.
[0024] After the reduction product is cooled, it is washed with cold water. During the washing process, the liquid-solid volume ratio is 1.00-1.05, and the washing temperature is 20°C. Wash, filter, and dry to obtain an intermediate product, and the filtered liquid is a chromium-free NaOH solution for recycling.
[0025] The intermediate product was dry-milled in a ball mill according to a ball-to-material ratio of 10:1, a rotational speed of 300 rpm / min, and a ball milling time of 60 minutes to obtain a ground product. The lining material of the ball mill is ZrO 2 , the ball is ZrO 2 ball.
[0026] The ground product is subjected to hydrothermal leaching in an autoclave, the leaching temperature is 220° C., the ...
Embodiment 3
[0030] The reduction of 1000g of sodium dichromate is carried out in a box-type reduction furnace, using hydrogen as the reducing gas, the reduction temperature is 550°C, the reduction time is 2h, and the hydrogen flow rate during the reduction process is 0.6L / min.
[0031] After the reduction product is cooled, it is washed with cold water. During the washing process, the liquid-solid volume ratio is 1.00-1.05, and the washing temperature is 20°C. Wash, filter, and dry to obtain an intermediate product, and the filtered liquid is a chromium-free NaOH solution for recycling.
[0032] The intermediate product was dry-milled in a ball mill according to a ball-to-material ratio of 5:1, a rotating speed of 300 rpm / min, and a ball milling time of 2 hours to obtain a milled product. The lining material of the ball mill is ZrO 2 , the ball is ZrO 2 ball.
[0033] The ground product is subjected to hydrothermal leaching in an autoclave, the leaching temperature is 180° C., the leac...
PUM
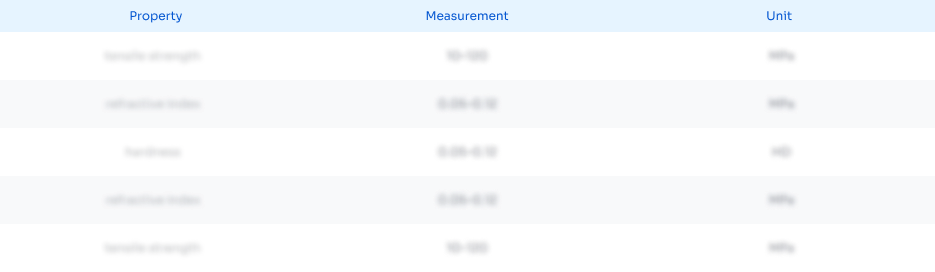
Abstract
Description
Claims
Application Information

- Generate Ideas
- Intellectual Property
- Life Sciences
- Materials
- Tech Scout
- Unparalleled Data Quality
- Higher Quality Content
- 60% Fewer Hallucinations
Browse by: Latest US Patents, China's latest patents, Technical Efficacy Thesaurus, Application Domain, Technology Topic, Popular Technical Reports.
© 2025 PatSnap. All rights reserved.Legal|Privacy policy|Modern Slavery Act Transparency Statement|Sitemap|About US| Contact US: help@patsnap.com