Vanadium manganese composite catalyst for removing nitrogen oxide in incineration gas and preparation method thereof
A composite catalyst, nitrogen oxide technology, applied in catalyst activation/preparation, metal/metal oxide/metal hydroxide catalyst, physical/chemical process catalyst, etc., to achieve a wide reaction temperature range, reduce reaction temperature, increase ratio The effect of surface area
- Summary
- Abstract
- Description
- Claims
- Application Information
AI Technical Summary
Problems solved by technology
Method used
Image
Examples
Embodiment 1
[0034] Embodiment 1: adopt solvothermal method
[0035]7 g of carbon nanotubes were added to 500 ml of absolute ethanol and 50 ml of nitric acid, and ultrasonically oscillated for 1 h to obtain a solution A. Add 350ml of tetrabutyl titanate into 700ml of absolute ethanol under the condition of ultrasonic oscillation, and shake for 1 hour to obtain solution B. Add 1 g of manganese acetate to 5 ml of acetic acid and 50 ml of absolute ethanol, shake for 1 h to obtain solution C. Add 0.6g of ammonium metavanadate and 1.2g of oxalic acid into 50ml of absolute ethanol, shake for 1h to obtain D solution. Mix solution C and solution D, slowly add it to solution B, then add it to solution A, shake it for 1-2 hours, put it into the reaction kettle, keep it at 230°C for 2 hours, cool it to room temperature, filter it with Wash with deionized water until neutral, dry and grind to obtain the catalyst. The phase composition of the catalyst see figure 1 , titanium dioxide exists in the a...
Embodiment 2
[0037] Embodiment 2: adopt solvothermal method
[0038] 7 g of carbon nanotubes were added to 500 ml of absolute ethanol and 50 ml of nitric acid, and ultrasonically oscillated for 1 h to obtain a solution A. Add 350ml of tetrabutyl titanate into 700ml of absolute ethanol under the condition of ultrasonic oscillation, and shake for 1 hour to obtain solution B. Add 10 g of manganese acetate to 50 ml of acetic acid and 50 ml of absolute ethanol, shake for 1 h to obtain solution C. Add 6g of ammonium metavanadate and 12g of oxalic acid into 50ml of absolute ethanol, shake for 1h to obtain D solution. Mix solution C and solution D, slowly add it to solution B, then add it to solution A, shake it for 1-2 hours, put it into the reaction kettle, keep it at 230°C for 2 hours, cool it to room temperature, filter it with Wash with deionized water until neutral, dry and grind to obtain the catalyst.
[0039] The obtained catalyst was mixed with 20% bentonite, added a small amount of w...
Embodiment 3
[0040] Embodiment 3: adopt solvothermal method
[0041] 7 g of carbon nanotubes were added to 500 ml of absolute ethanol and 50 ml of nitric acid, and ultrasonically oscillated for 1 h to obtain a solution A. Add 350ml of tetrabutyl titanate into 700ml of absolute ethanol under the condition of ultrasonic oscillation, and shake for 1 hour to obtain solution B. Add 20g of manganese acetate to 100ml of acetic acid and 50ml of absolute ethanol, shake for 1h to obtain C solution. Add 12g of ammonium metavanadate and 24g of oxalic acid into 50ml of absolute ethanol, shake for 1h to obtain D solution. Mix solution C and solution D, slowly add it to solution B, then add it to solution A, shake it for 1-2 hours, put it into the reaction kettle, keep it at 230°C for 2 hours, cool it to room temperature, filter it with Wash with deionized water until neutral, dry and grind to obtain the catalyst.
[0042] The obtained catalyst was mixed with 20% bentonite, added a small amount of wat...
PUM
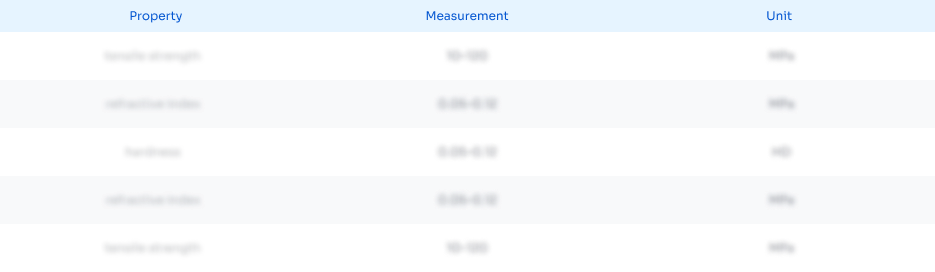
Abstract
Description
Claims
Application Information

- R&D
- Intellectual Property
- Life Sciences
- Materials
- Tech Scout
- Unparalleled Data Quality
- Higher Quality Content
- 60% Fewer Hallucinations
Browse by: Latest US Patents, China's latest patents, Technical Efficacy Thesaurus, Application Domain, Technology Topic, Popular Technical Reports.
© 2025 PatSnap. All rights reserved.Legal|Privacy policy|Modern Slavery Act Transparency Statement|Sitemap|About US| Contact US: help@patsnap.com