Method for arsenic removal and phosphorous removal out of iron-containing materials
A technology of iron-containing raw materials and concentrated alkali, which is applied in the direction of improving process efficiency and can solve problems such as high cost and long duration
- Summary
- Abstract
- Description
- Claims
- Application Information
AI Technical Summary
Problems solved by technology
Method used
Image
Examples
Embodiment 1
[0033] 1160g of pre-reduced iron ore pellets were divided into the following particles:
[0034] 221 g of Particle 1 (-0.25 mm), containing (wt%): (Fe+Mn) = 94.8; CaO·SiO2 = 4.2; V = 0.15; Y = 0.17; As = 0.15.
[0035] 519g particle 2 (-0.25mm+0.08mm), comprising (wt%): (Fe+Mn)=61.4; CaO·SiO2=3.7; SiO2=8.1; Al2O3=5.4; V=0.05; Y=0.07; Ni= 0.11; As=0.22; Zr=0.05.
[0036] 420 g of particle 3 (-0.08 mm), ie waste, contained (wt%): (Fe+Mn) = 12.7; As = 0.35, same silicate and coke.
[0037] 519g particle 2 is transferred to steel ball mill, in steel ball mill, add 248g NaCl, 770g water and 3g caustic soda (sodium hydroxide) to solution pH=12 (solid phase and liquid ratio S: L=1: 1, the NaCl concentration is 24.36wt%), then ground for about 2h; the suspension obtained is separated from the pulverizer and filtered to a humidity of 30.4wt%; the filter residue is washed with 158g of NaCl solution with a concentration of 24.36wt% (NaCl The amount of the solution is equal to the wate...
Embodiment 2
[0040] 1000 g of iron-containing pellets were transferred to a steel ball mill. Dissolve 250g NaCl in 1000g water. In the obtained 20% NaCl solution, 5 g of NaOH was added to make pH=12. NaCl lye was added to the crushed iron-containing pellets (S:L=1:1.25). The solid raw material was ground for about 2 hours. The resulting suspension separated from solution. The residue with a humidity of 29.1% was washed with 291 g of 20% NaCl solution and then with 1000 g of water. The solid residue was separated from the suspended particles and dried to obtain 621g iron ore solution, which contained (wt%):
[0041] (Fe+Mn)=67.1; Y=0.1; V=0.1; Ni=0.1; As=0.08; P=0.16.
Embodiment 3
[0043] Mix 1000g of iron ore powder with coke powder; place the resulting mixture under reducing conditions at 1300°C in the presence of an iron reducing agent. The resulting 1105 g lump was dry ground and sieved through a No. 0063 sieve. The following substances were obtained:
[0044] 1.606 g of iron-containing raw material (wt %) in the form of -3+0.5mm granules and -0.08mm powder:
[0045] (Fe+Mn) = 89.8; As = 0.23; P = 0.48.
[0046] 2.591g-0.08mm grade silicate and slag, including (Fe+Mn) = 12.7%, and
[0047] 3.8g irreversible loss during the separation process.
[0048] Transfer 606g of granular iron-containing raw materials to a steel ball mill, add 606g of water, 180g of NaCl and 3g of NaOH, and grind for about 2 hours. A suspension of solid particles on the order of -0.38 mm was obtained and filtered. 179 g of solid residue with a humidity of 29.5% were washed with 20% NaCl solution at pH 1.5 and then with 606 g of water. The resulting residue was mixed with 1...
PUM
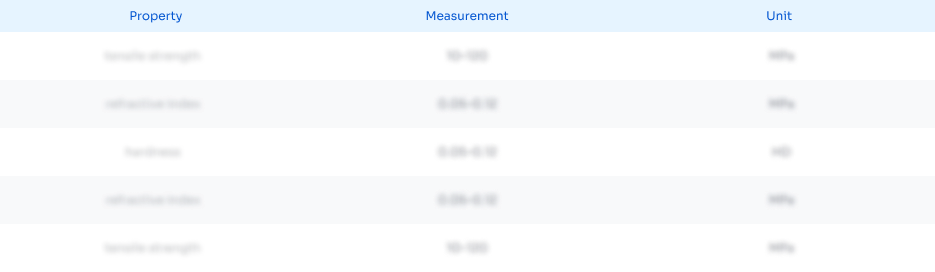
Abstract
Description
Claims
Application Information

- R&D
- Intellectual Property
- Life Sciences
- Materials
- Tech Scout
- Unparalleled Data Quality
- Higher Quality Content
- 60% Fewer Hallucinations
Browse by: Latest US Patents, China's latest patents, Technical Efficacy Thesaurus, Application Domain, Technology Topic, Popular Technical Reports.
© 2025 PatSnap. All rights reserved.Legal|Privacy policy|Modern Slavery Act Transparency Statement|Sitemap|About US| Contact US: help@patsnap.com