Recovery method of molybdenum concentrates
A recovery method and technology for molybdenum concentrate, applied in chemical instruments and methods, molybdenum compounds, rhenium compounds, etc., can solve the problems of large alkali consumption, large oxygen consumption, low sulfuric acid concentration in leachate, etc., to improve recovery rate, reduce Effects of Environmental Pollution
- Summary
- Abstract
- Description
- Claims
- Application Information
AI Technical Summary
Problems solved by technology
Method used
Examples
Embodiment 1
[0018] This embodiment provides a method for comprehensive utilization of molybdenum, rhenium, copper, and sulfur in a combined high-pressure oxidation-flotation process for the problems existing in the prior art.
[0019] The method comprises: carrying out high-temperature oxygen pressure leaching autothermal reaction of molybdenum concentrate under alkaline conditions, controlling the reaction speed by adjusting the oxygen partial pressure without external heating. Add 90-130 times the theoretical amount of sodium hydroxide, the reaction temperature is 140-170°C, and the high-temperature oxygen pressure leaching time is 1-3 hours. The self-heating oxidized slag is returned to the flotation system, and the molybdenum concentrate is obtained by one-time roughing, one-time sweeping and four-time beneficiation, and the metal copper in the flotation tailings is recovered by acid leaching. Molybdenum concentrate and oxide slag flotation concentrate are blended according to the rat...
Embodiment 2
[0023] Molybdenum concentrate contains molybdenum 42.70%, Cu 3.52%, Re 0.0015%, S 34.15%, SiO 2 4.41%.
[0024] Take 120g of molybdenum concentrate and 140g of sodium hydroxide for autothermal leaching for 1.5h under the conditions of liquid-solid ratio 7 and temperature 140℃, the total pressure is controlled at 1.6MPa, and the solid-liquid separation is achieved by filtration; The fine open circuit flotation process test obtained a molybdenum concentrate with a molybdenum content of 34.22% and a yield of 14.30%. The obtained oxide slag flotation molybdenum concentrate and the original molybdenum concentrate were blended in a ratio of 1:1 for autothermal leaching; the flotation tailings molybdenum The grade is reduced to 0.36%, and acid leaching is carried out at a sulfuric acid concentration of 80g / L to prepare copper sulfate; ammonium molybdate and ammonium perrhenate products are produced from the leaching solution, and sodium sulfate is prepared by evaporation and crystall...
Embodiment 3
[0026] Molybdenite concentrate contains molybdenum 43.94%, Cu 1.07%, Re 0.0016%, S 31.75%, SiO 2 7.53%.
[0027] Take 120g of molybdenum concentrate and 120g of sodium hydroxide to conduct autothermal leaching for 1.5h under the condition of liquid-solid ratio 7 and temperature 160℃, the total pressure is controlled at 1.6MPa, and the solid-liquid separation is achieved by filtration; The refined open-circuit flotation process test obtained a molybdenum concentrate with a molybdenum content of 36.30% and a yield of 15.30%. The obtained oxide slag flotation molybdenum concentrate and the original molybdenum concentrate were mixed in a ratio of 1:1 for autothermal leaching; the flotation tailings molybdenum The grade is reduced to 0.40%, acid leaching is carried out at a sulfuric acid concentration of 50g / L to prepare copper sulfate; ammonium molybdate and ammonium perrhenate products are produced from the leaching solution, and sodium sulfate is prepared by evaporation and cry...
PUM
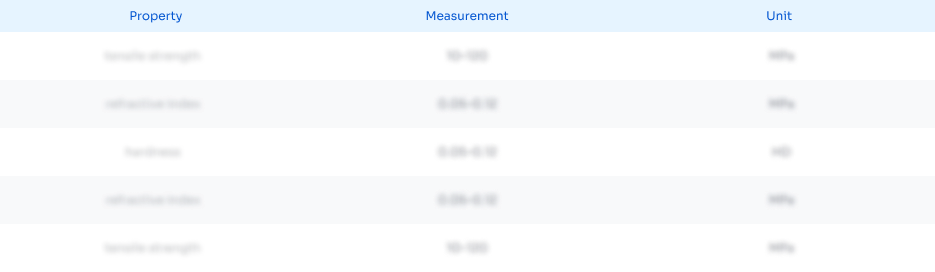
Abstract
Description
Claims
Application Information

- R&D
- Intellectual Property
- Life Sciences
- Materials
- Tech Scout
- Unparalleled Data Quality
- Higher Quality Content
- 60% Fewer Hallucinations
Browse by: Latest US Patents, China's latest patents, Technical Efficacy Thesaurus, Application Domain, Technology Topic, Popular Technical Reports.
© 2025 PatSnap. All rights reserved.Legal|Privacy policy|Modern Slavery Act Transparency Statement|Sitemap|About US| Contact US: help@patsnap.com