Method for eliminating chlorine-containing volatile organic compound by low-temperature catalytic combustion
An organic compound and volatile technology, applied in the direction of combustion methods, combustion types, incinerators, etc., can solve the problems of easy loss of catalyst active components, low catalytic combustion activity, short catalyst life, etc., and achieve a convenient and practical technical route. High catalytic activity and strong resistance to chlorine poisoning
- Summary
- Abstract
- Description
- Claims
- Application Information
AI Technical Summary
Problems solved by technology
Method used
Examples
Embodiment 1
[0024] Commercially available 80mL tetrabutyl titanate Ti(OC 4 h 9 ) 4 , 320mL of absolute ethanol, 4mL of glacial acetic acid were mixed as solution A; 20mL of deionized water, 160mL of absolute ethanol, and 2mL of concentrated hydrochloric acid were mixed as solution B; under vigorous stirring, solution B was added dropwise to solution A, and Stir at a temperature of 60-70°C to form a transparent, stable light yellow sol, and then seal and age to form a gel. The gel was placed in an oven and dried at 70° C. for 12 hours to obtain a xerogel. Move the dry gel to a muffle furnace for calcination: the specific calcination process is: start heating at 50°C, program the temperature at a rate of 10°C / min, and maintain it at 480°C for 5 hours to obtain TiO 2 . After removal, the catalyst was pulverized to ensure that the catalyst was in powder form.
[0025] 0.386g ammonium metavanadate NH 4 VO 3 , 1.857g oxalic acid C 2 h 2 o 4 2H 2 O was added to 10mL deionized water, s...
Embodiment 2
[0027] 0.193g ammonium metavanadate NH 4 VO 3 , 0.929g oxalic acid C 2 h 2 o 4 2H 2 O was added to 10mL deionized water, stirred and mixed to prepare an impregnation solution, and added to 10g of commercially available titanium oxide TiO 2 , stirred until the impregnating solution is completely absorbed, let stand at room temperature for 12 hours, and then dried at 100°C for 12 hours. Catalyst roasting is the same as embodiment 1.1.5%VOx / TiO 2 . After taking it out, the powder catalyst is pressed into tablets, and after grinding, 40-60 mesh particles are screened.
Embodiment 3
[0029] 0.736g ammonium metavanadate NH 4 VO 3 , 3.714g oxalic acid C 2 h 2 o 4 2H 2 O was added to 10mL deionized water, stirred and mixed to prepare an impregnation solution, and added to 10g of commercially available titanium oxide TiO 2 , stirred until the impregnating solution is completely absorbed, let stand at room temperature for 12 hours, and then dried at 100°C for 12 hours. Catalyst roasting is the same as embodiment 1. 6%VOx / TiO 2 . After taking it out, the powder catalyst is pressed into tablets, and after grinding, 40-60 mesh particles are screened.
PUM
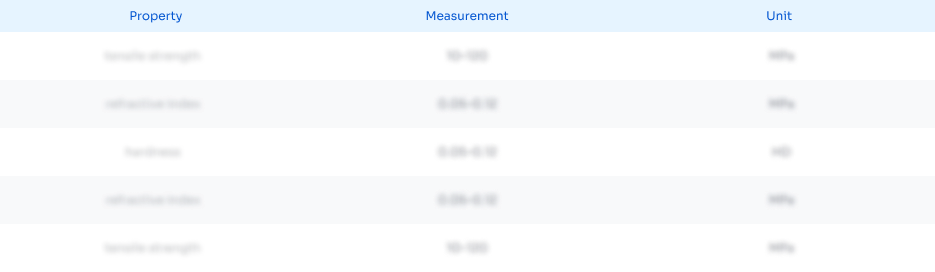
Abstract
Description
Claims
Application Information

- Generate Ideas
- Intellectual Property
- Life Sciences
- Materials
- Tech Scout
- Unparalleled Data Quality
- Higher Quality Content
- 60% Fewer Hallucinations
Browse by: Latest US Patents, China's latest patents, Technical Efficacy Thesaurus, Application Domain, Technology Topic, Popular Technical Reports.
© 2025 PatSnap. All rights reserved.Legal|Privacy policy|Modern Slavery Act Transparency Statement|Sitemap|About US| Contact US: help@patsnap.com