Method for recycling metal oxide from waste flue gas denitration catalyst
A denitration catalyst and waste flue gas technology, which is applied in the field of non-ferrous metal recovery, can solve the problems such as comprehensive recovery of waste SCR flue gas denitration catalysts that cannot be used, and achieve the effects of rapid recycling, cost reduction and simple process
- Summary
- Abstract
- Description
- Claims
- Application Information
AI Technical Summary
Problems solved by technology
Method used
Image
Examples
Embodiment 1
[0046] Embodiment 1: as figure 1 Shown: the method for recovering metal oxides from waste flue gas denitrification catalyst in this embodiment is carried out according to the following steps.
[0047] Pre-roasting of raw materials: Take the expired honeycomb waste flue gas denitrification catalyst and put it into the rotary kiln, and perform high-temperature roasting at about 650 ℃ to remove Hg, As and organic impurities that may be adsorbed on the surface, and keep the temperature for 4 hours.
[0048] Mixing and crushing: adding Na to the roasted waste flue gas denitrification catalyst 2 CO 3 , Na 2 CO 3 and waste flue gas denitrification catalyst (by TiO 2 The molar ratio of the powder is 2:1. After being fully mixed by a mixer, it is put into a crusher for crushing and grinding until the particle size is ≤200 μm to obtain a mixed powder.
[0049] Sodium roasting: Put the mixed and crushed mixed powder into the rotary kiln for high-temperature roasting at 650-700 °C, a...
Embodiment 2
[0054] Embodiment 2: as figure 1 Shown: the method for recovering metal oxides from waste flue gas denitrification catalyst in this embodiment is carried out according to the following steps.
[0055] Pre-roasting of raw materials: Take the expired honeycomb waste flue gas denitrification catalyst and put it into the rotary kiln, and perform high-temperature roasting at about 650 ℃ to remove Hg, As and organic impurities that may be adsorbed on the surface, and keep the temperature for 3 hours.
[0056] Mixing and crushing: adding Na to the roasted waste flue gas denitrification catalyst 2 CO 3 , Na 2 CO 3 and waste flue gas denitrification catalyst (by TiO 2 The molar ratio is 2.5:1. After being fully mixed by a mixer, it is put into a crusher for crushing and grinding until the particle size is ≤200 μm to obtain a mixed powder.
[0057]Sodium roasting: Put the mixed and pulverized mixed powder into a rotary kiln for high-temperature roasting at 650-700 °C, and keep the ...
Embodiment 3
[0062] Embodiment 3: as figure 1 Shown: the method for recovering metal oxides from waste flue gas denitrification catalyst in this embodiment is carried out according to the following steps.
[0063] Pre-roasting of raw materials: Take the expired honeycomb waste flue gas denitration catalyst and put it into the rotary kiln, and perform high-temperature roasting at about 650 ℃ to remove Hg, As and organic impurities that may be adsorbed on the surface, and keep the temperature constant for 2 hours.
[0064] Mixing and crushing: adding Na to the roasted waste flue gas denitrification catalyst 2 CO 3 , Na 2 CO 3 and waste flue gas denitrification catalyst (by TiO 2 The molar ratio of the powder is 3:1. After being fully mixed by a mixer, it is put into a crusher for crushing and grinding until the particle size is ≤200 μm to obtain a mixed powder.
[0065] Sodium roasting: Put the mixed and pulverized powder into the rotary kiln for high-temperature roasting at 650-700 °C,...
PUM
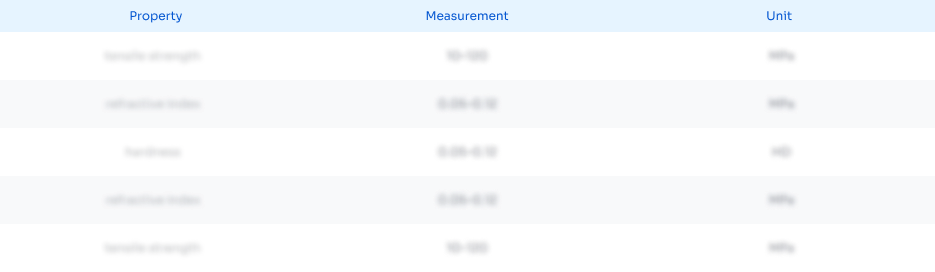
Abstract
Description
Claims
Application Information

- R&D
- Intellectual Property
- Life Sciences
- Materials
- Tech Scout
- Unparalleled Data Quality
- Higher Quality Content
- 60% Fewer Hallucinations
Browse by: Latest US Patents, China's latest patents, Technical Efficacy Thesaurus, Application Domain, Technology Topic, Popular Technical Reports.
© 2025 PatSnap. All rights reserved.Legal|Privacy policy|Modern Slavery Act Transparency Statement|Sitemap|About US| Contact US: help@patsnap.com