Method for preparing composite material pressure container with PbSn alloy lining by plasma spray
A technology for pressure vessels and composite materials, applied in the field of materials, can solve the problems of heavy quality of pressure vessels, and achieve the effects of saving costs, increasing the number of repeated uses, and having a small porosity
- Summary
- Abstract
- Description
- Claims
- Application Information
AI Technical Summary
Problems solved by technology
Method used
Image
Examples
specific Embodiment approach 1
[0013] Specific implementation mode one: the following combination figure 1 Describe this embodiment, the method of this embodiment includes the following steps:
[0014] Step 1, preparing a winding layer of carbon fiber wound composite material impregnated with epoxy resin on a mandrel conforming to the shape of the pressure vessel;
[0015] Step 2, preparing a resin transition layer doped with metal powder on the inner wall of the carbon fiber wound composite winding layer;
[0016] Step 3, curing the resin transition layer doped with metal powder;
[0017] Step 4: Prepare the inner lining layer of the pressure vessel by plasma spraying on the inner wall of the cured resin transition layer.
[0018] Step 1 The process of preparing the winding layer of carbon fiber wound composite material impregnated with epoxy resin is as follows:
[0019] Step a, immerse the carbon fiber in the epoxy resin, so that the surface of the carbon fiber is fully adhered to the epoxy resin;
...
specific Embodiment approach 2
[0035] Embodiment 2: The difference between this embodiment and Embodiment 1 is that the parameters of plasma spraying are: spraying power is 30kW-45kW, working current is 280A-350A, working gas flow is 30L / min-45L / min. The flow rate of the powder gas is 1.0L / min~2.5L / min, and the others are the same as the first embodiment.
specific Embodiment approach 3
[0036] Embodiment 3: The difference between this embodiment and Embodiment 1 is that the plasma spraying parameters are: the spraying power is 40kW, the working current is 300A, the working gas flow rate is 40L / min, the powder feeding gas flow rate is 2.0L / min, Others are the same as the first embodiment.
PUM
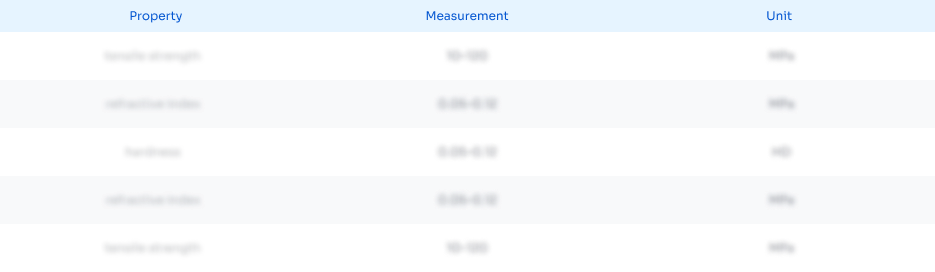
Abstract
Description
Claims
Application Information

- R&D
- Intellectual Property
- Life Sciences
- Materials
- Tech Scout
- Unparalleled Data Quality
- Higher Quality Content
- 60% Fewer Hallucinations
Browse by: Latest US Patents, China's latest patents, Technical Efficacy Thesaurus, Application Domain, Technology Topic, Popular Technical Reports.
© 2025 PatSnap. All rights reserved.Legal|Privacy policy|Modern Slavery Act Transparency Statement|Sitemap|About US| Contact US: help@patsnap.com