Polyamide composite reverse osmosis membrane containing nano materials
A technology of reverse osmosis membrane and nanomaterials, which is applied in the field of polyamide composite reverse osmosis membrane, can solve the problems of poor anti-pollution ability, short service life of the membrane, resistance to oxidation, etc. increased effect
- Summary
- Abstract
- Description
- Claims
- Application Information
AI Technical Summary
Problems solved by technology
Method used
Image
Examples
Embodiment 1
[0016] Example 1: The polysulfone solution was prepared according to 15 kg of polysulfone: 74.5 kg of dimethylacetamide (DMAC): 10 kg of ethylene glycol dimethyl ether (DMPE), and 0.5 kg of nano silicon oxide.
[0017] The prepared polysulfone solution is coated on the non-woven fabric, and then the interface reaction is carried out on the polysulfone layer to form an aromatic polyamide layer, and finally a layer of electrically neutral coating is coated on the polyamide layer to form a polyamide composite reaction. permeable membrane.
[0018] The polyamide composite reverse osmosis membrane prepared above was used as water inflow of 2000ppm NaCl aqueous solution, and the initial performance test was carried out under the conditions of 25°C, pH value of 7.5, and pressure of 225psi, and then operated under the above conditions for 72 hours. Its performance, the results are shown in Table 1.
[0019] Table 1
[0020]
Embodiment 2
[0022] According to polysulfone 40kg: dimethylacetamide (DMAC), dimethylformamide (DMF), the arbitrary ratio mixture 140kg of N methylpyrrolidone (NMP) and dimethyl sulfoxide (DMSO); Polyethylene glycol ( PEG), polyvinylpyrrolidone (PVP), ethylene glycol dimethyl ether (DMPE), polyvinyl alcohol (PVA) in any ratio mixture 30kg; nano-titanium oxide, nano-zinc oxide, nano-alumina, nano-iron oxide, nano-oxide The polysulfone solution was prepared with 40 kg of any mixture of silicon and nano-calcium oxide.
[0023] The prepared polysulfone solution is coated on the non-woven fabric, and then the interface reaction is carried out on the polysulfone layer to form an aromatic polyamide layer, and finally a layer of electrically neutral coating is coated on the polyamide layer to form a polyamide composite reaction. permeable membrane.
[0024] Examples 3-11 prepared polysulfone solution according to the proportion shown in Table 2, and the method for preparing polyamide composite re...
PUM
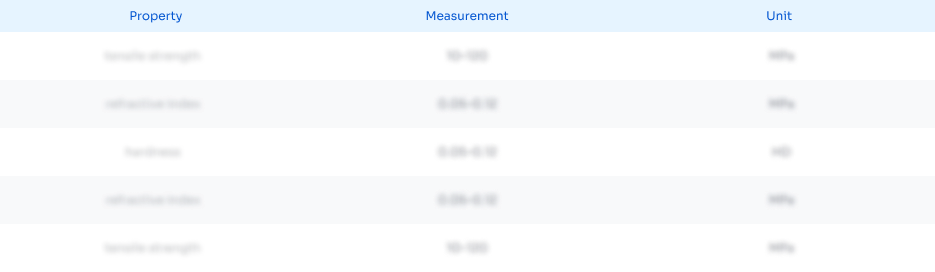
Abstract
Description
Claims
Application Information

- R&D
- Intellectual Property
- Life Sciences
- Materials
- Tech Scout
- Unparalleled Data Quality
- Higher Quality Content
- 60% Fewer Hallucinations
Browse by: Latest US Patents, China's latest patents, Technical Efficacy Thesaurus, Application Domain, Technology Topic, Popular Technical Reports.
© 2025 PatSnap. All rights reserved.Legal|Privacy policy|Modern Slavery Act Transparency Statement|Sitemap|About US| Contact US: help@patsnap.com