High-toughness wear-resistant polyformaldehyde composition and preparation method thereof
A polyoxymethylene compound, high wear-resistant technology, applied in the field of polyoxymethylene compound and its preparation, can solve the damage of mechanical properties such as tensile strength and flexural strength, limit the application of polyoxymethylene modified products, and the impact resistance of polyoxymethylene limited and other problems, to achieve the effect of improving wear resistance, high toughness and wear resistance, and reducing wear rate
- Summary
- Abstract
- Description
- Claims
- Application Information
AI Technical Summary
Problems solved by technology
Method used
Examples
example 1
[0024] Take polyoxymethylene copolymer, polyethylene oxide, polytetrafluoroethylene fiber, antioxidant, formaldehyde absorbent, and blend all raw materials according to the following composition and mass percentage:
[0025] Polyoxymethylene 84.4wt.%
[0026] Polyethylene oxide 10.0wt.%
[0027] PTFE fiber 5.0wt.%
[0028] Antioxidant 1010 0.25wt.%
[0029] Antioxidant 168 0.25wt.%
[0030] Dicyandiamide 0.1wt.%
[0031] The components in the above ratio are placed in a mixer and fully mixed, and then the mixture is melt-blended, extruded, cooled and granulated through a twin-screw extruder granulator. The barrel temperature is 170°C, 172°C, 175°C, 173°C respectively, and the head temperature is set at 175°C. Wherein, during the extrusion process, the screw speed is 190 rpm, the melt pressure is 40 MPa, and the torque is 60 N·m. The prepared pellets were fully dried in a vacuum oven at 80°C, and injected into standard mechanical property test specimens and friction test sp...
example 2
[0033] Take polyoxymethylene copolymer, polyethylene oxide, polytetrafluoroethylene fiber, antioxidant, formaldehyde absorbent, and blend all raw materials according to the following composition and mass percentage:
[0034] Polyoxymethylene 79.4wt.%
[0035] Polyethylene oxide 10.0wt.%
[0036] PTFE fiber 10.0wt.%
[0037] Antioxidant 1010 0.25wt.%
[0038] Antioxidant 168 0.25wt.%
[0039] Dicyandiamide 0.1wt.%
[0040] The components in the above ratio are placed in a mixer and fully mixed, and then the mixture is melt-blended, extruded, cooled and granulated through a twin-screw extruder granulator. The barrel temperature is 170°C, 172°C, 175°C, 173°C respectively, and the head temperature is set at 175°C. Wherein, during the extrusion process, the screw speed is 190 rpm, the melt pressure is 40 MPa, and the torque is 60 N·m. The prepared pellets were fully dried in a vacuum oven at 80°C, and injected into standard mechanical property test specimens and friction test...
example 3
[0042] Get homopolyoxymethylene, polyoxyethylene, polytetrafluoroethylene fiber, antioxidant, formaldehyde absorbent, and blend all raw materials according to the following composition and mass percentage:
[0043] Polyoxymethylene 74.4wt.%
[0044] Polyethylene oxide 15.0wt.%
[0045] PTFE fiber 10.0wt.%
[0046] Antioxidant 1010 0.25wt.%
[0047] Antioxidant 168 0.25wt.%
[0048] Dicyandiamide 0.1wt.%
[0049] The components in the above ratio are placed in a mixer and fully mixed, and then the mixture is melt-blended, extruded, cooled and granulated through a twin-screw extruder granulator. The barrel temperature is 170°C, 172°C, 175°C, 173°C respectively, and the head temperature is set at 175°C. Wherein, during the extrusion process, the screw speed is 190 rpm, the melt pressure is 40 MPa, and the torque is 60 N·m. The prepared pellets were fully dried in a vacuum oven at 80°C, and injected into standard mechanical property test specimens and friction test specimens...
PUM
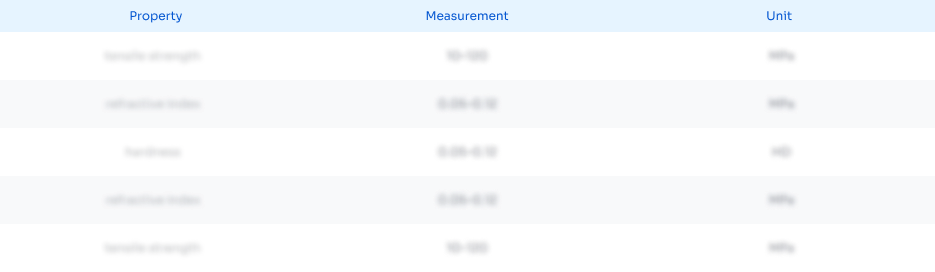
Abstract
Description
Claims
Application Information

- R&D
- Intellectual Property
- Life Sciences
- Materials
- Tech Scout
- Unparalleled Data Quality
- Higher Quality Content
- 60% Fewer Hallucinations
Browse by: Latest US Patents, China's latest patents, Technical Efficacy Thesaurus, Application Domain, Technology Topic, Popular Technical Reports.
© 2025 PatSnap. All rights reserved.Legal|Privacy policy|Modern Slavery Act Transparency Statement|Sitemap|About US| Contact US: help@patsnap.com