Preparation method of Al-Cu-Mg-Ag ultrafine crystal heat-resistant aluminum alloy
An al-cu-mg-ag, ultra-fine grain technology, applied in the field of metallurgy, to achieve the effect of improving overall strength and high temperature heat resistance, simple process and convenient operation
- Summary
- Abstract
- Description
- Claims
- Application Information
AI Technical Summary
Problems solved by technology
Method used
Image
Examples
Embodiment 1
[0020] The chemical composition of the alloy is: Al-5.3Cu-0.8Mg-0.6Ag-0.1Zr-0.3Mn (mass fraction) alloy ingredients (raw materials are: A00 pure aluminum, Al-50Cu master alloy, No. 2 industrial pure magnesium, 99.9% Silver, Al-10Mn master alloy, Al-4Zr master alloy) were smelted in a medium-frequency induction resistance furnace, and used C 2 Cl 6 Carry out scouring treatment, after standing still, remove slag, and cast into a round billet through an iron mold, 450? After homogenization treatment for 24 hours, at 390? Hot extrusion was carried out with an extrusion ratio of 12. The hot-extruded alloy is deformed by equal-diameter angular hot-extrusion. The die of equal-diameter angular extrusion adopts a right-angle equal-channel extrusion die. The extrusion temperature is 390 ° C and the extrusion passes are 6 times. After each equal diameter angular extrusion, put it into a furnace to heat to the extrusion temperature and keep it warm for 30 minutes, and then perform the ...
Embodiment 2
[0022]Adopt the billet of embodiment 1, 470? After homogenization treatment for 48 hours, at 430? Hot extrusion was carried out with an extrusion ratio of 8. The alloy in the extruded state is deformed by equal-diameter angular hot extrusion. The die of equal-diameter angular extrusion adopts a right-angle equal-channel extrusion die, the extrusion temperature is 430 ° C, and the extrusion passes are 4 times. After each equal diameter angular extrusion, put it into a furnace to heat to the extrusion temperature and keep it warm for 60 minutes, and then perform the next equal diameter angular extrusion. Turn 90° after each equal radial angle extrusion for the next equal diameter angle extrusion. After equal diameter hot extrusion, it was solution treated at 535°C for 6h, quenched in water at room temperature, and then aged at 150°C for 40h. The room temperature hardness and high temperature heat resistance properties of the alloy are shown in Table 1.
Embodiment 3
[0024] Adopt the billet of embodiment 1, 420? After homogenization treatment for 35h, at 350? Hot extrusion was carried out with an extrusion ratio of 15. The alloy in the extruded state is deformed by equal-diameter angular hot extrusion. The die of equal-diameter angular extrusion adopts a right-angle equal-channel extrusion die. The extrusion temperature is 350 ° C and the extrusion passes are 8 times. After each equal diameter angular extrusion, put it into a furnace to heat to the extrusion temperature and keep it warm for 10 minutes, and then perform the next equal diameter angular extrusion. Turn 90° after each equal radial angle extrusion for the next equal diameter angle extrusion. After equal diameter hot extrusion at 520? After 24 hours of solid solution, quenched into water at room temperature, at 210? Carry out artificial aging treatment for 5h. The room temperature hardness and high temperature heat resistance properties of the alloy are shown in Table 1.
PUM
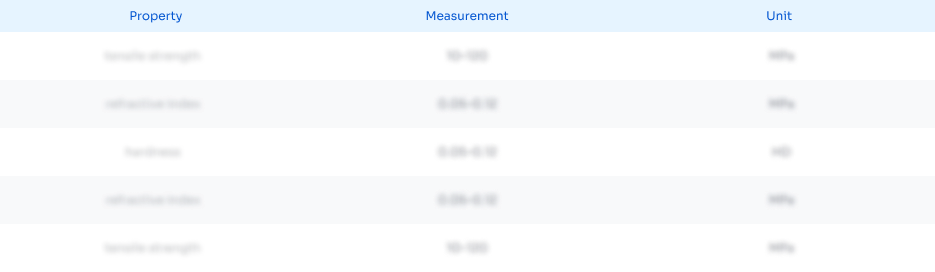
Abstract
Description
Claims
Application Information

- R&D
- Intellectual Property
- Life Sciences
- Materials
- Tech Scout
- Unparalleled Data Quality
- Higher Quality Content
- 60% Fewer Hallucinations
Browse by: Latest US Patents, China's latest patents, Technical Efficacy Thesaurus, Application Domain, Technology Topic, Popular Technical Reports.
© 2025 PatSnap. All rights reserved.Legal|Privacy policy|Modern Slavery Act Transparency Statement|Sitemap|About US| Contact US: help@patsnap.com