Finite element modeling method for predicting forging force in rotary swaging process
A modeling method and finite element technology, applied in special data processing applications, instruments, electrical digital data processing, etc., can solve problems such as heavy workload and long time consumption
- Summary
- Abstract
- Description
- Claims
- Application Information
AI Technical Summary
Problems solved by technology
Method used
Image
Examples
Embodiment Construction
[0044] Flow chart of the present invention sees figure 1 . Below in conjunction with accompanying drawing, take the prediction of the forging pressure of pure magnesium swaging process as example, specifically illustrate the method of the present invention, but protection scope of the present invention is not limited to following embodiment:
[0045] Step 1: Collect the original technical parameters of swaging, including: spindle speed of swaging machine, feeding speed, number of rollers in the machine head, diameter of incoming material, diameter after swaging, length of compression zone, length of sizing belt, cone The feed angle and initial swaging temperature are shown in Table 1.
[0046] Table 1 Calculate the original technical parameters required for swaging forging pressure
[0047]
[0048] Step 2: Use the mathematical software matlab to calculate the curves of the radial and axial movement trajectories of the swaging die relative to the workpiece to be swaged, a...
PUM
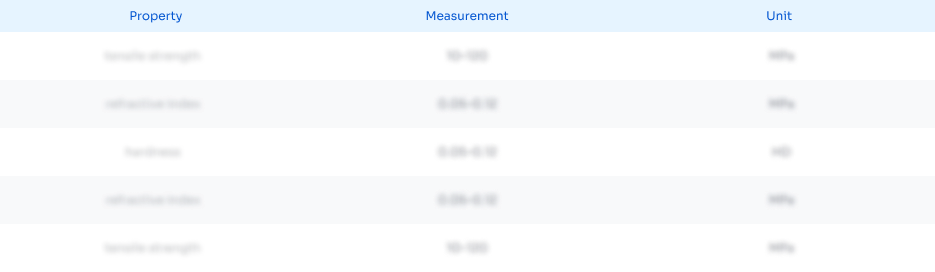
Abstract
Description
Claims
Application Information

- Generate Ideas
- Intellectual Property
- Life Sciences
- Materials
- Tech Scout
- Unparalleled Data Quality
- Higher Quality Content
- 60% Fewer Hallucinations
Browse by: Latest US Patents, China's latest patents, Technical Efficacy Thesaurus, Application Domain, Technology Topic, Popular Technical Reports.
© 2025 PatSnap. All rights reserved.Legal|Privacy policy|Modern Slavery Act Transparency Statement|Sitemap|About US| Contact US: help@patsnap.com