Nanometer butadiene-styrene-vinyl pyridine rubber modified epoxy resin and production method thereof
A technology of styrene-butadiene rubber and epoxy resin, which is applied in the field of nano-styrene-butadiene pyridine rubber modified epoxy resin and its production, can solve the problems of decreased thermal deformation temperature, poor quality stability, large capital investment, etc., and achieves high toughness High temperature resistance, improved impact strength, and less technical difficulty
- Summary
- Abstract
- Description
- Claims
- Application Information
AI Technical Summary
Problems solved by technology
Method used
Image
Examples
Embodiment Construction
[0013] Accompanying drawing is the production process reference figure of the present invention, and the production method of a kind of nano styrene-butadiene rubber modified epoxy resin of the present invention is as follows:
[0014] The first step: Mix the nano-styrene-butadiene pyrene rubber in the component with the dispersant, and perform pre-dispersion by anchor stirring with temperature control and speed regulation after activation. The temperature is controlled at 30-40°C, the stirring speed is 800-1000 revolutions per minute, and the time is two minutes.
[0015] Step 2: Add epoxy resin, coupling agent, defoamer, leveling agent and accelerator to the material after the first step according to the component ratio for pre-soaking.
[0016] Step 3: Grind and roughly disperse the pre-soaked material in the second step.
[0017] The fourth step: Grinding and finely dispersing the materials after the third step.
[0018] The fifth step: finely disperse the material after...
PUM
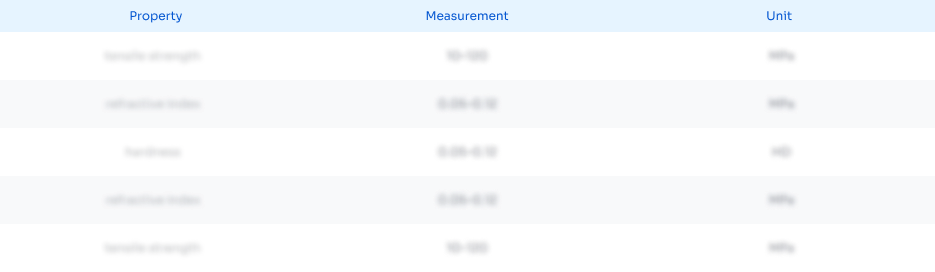
Abstract
Description
Claims
Application Information

- R&D
- Intellectual Property
- Life Sciences
- Materials
- Tech Scout
- Unparalleled Data Quality
- Higher Quality Content
- 60% Fewer Hallucinations
Browse by: Latest US Patents, China's latest patents, Technical Efficacy Thesaurus, Application Domain, Technology Topic, Popular Technical Reports.
© 2025 PatSnap. All rights reserved.Legal|Privacy policy|Modern Slavery Act Transparency Statement|Sitemap|About US| Contact US: help@patsnap.com