Alkali leaching method of zinc oxide mine
A zinc oxide ore and alkali leaching technology, applied in the direction of improving process efficiency, can solve the problems of difficult to effectively separate leaching solution and leaching slag, many types of impurities, low zinc leaching rate, etc., achieving easy control of leaching conditions and reducing production costs , the effect of less types of impurities
- Summary
- Abstract
- Description
- Claims
- Application Information
AI Technical Summary
Problems solved by technology
Method used
Image
Examples
Embodiment 1
[0030] Finely grind the zinc oxide raw ore to -100 mesh, calcinate at 400 ° C for 2 hours, take 1 gram after cooling and immerse in 80 ml of NaOH solution with a mass fraction of 20% (concentration: 6.25 mol / L), and control the temperature at 100 ° C. Stir for 4 hours, and use high-speed centrifugation to separate solid and liquid after cooling to obtain a solution containing zinc.
[0031] The leaching solution was fixed to a volume of 250 milliliters, and the concentration of zinc in it was detected after acidification and dilution, and it was calculated that after the zinc oxide raw ore was calcined at 400°C, the zinc leaching rate of alkali leaching was 92.88%.
Embodiment 2
[0033] Finely grind the zinc oxide raw ore to -100 mesh, calcinate at 500 ° C for 2 hours, take 1 gram after cooling and immerse in 80 ml of NaOH solution with a mass fraction of 15% (concentration: 4.41 mol / L), and control the temperature at 100 ° C. Stir for 4 hours, and use high-speed centrifugation to separate solid and liquid after cooling to obtain a solution containing zinc.
[0034] The leaching solution was fixed to a volume of 250 milliliters, and the concentration of zinc in it was detected after acidification and dilution, and it was calculated that after the zinc oxide raw ore was calcined at 500°C, the zinc leaching rate of alkali leaching was 87.55%.
Embodiment 3
[0036] Finely grind the zinc oxide raw ore to -100 mesh, calcinate at 600 ° C for 2 hours, take 1 gram after cooling and immerse in 80 ml of NaOH solution with a mass fraction of 17% (concentration: 5.12 mol / L), and control the temperature at 80 ° C. Stir for 4 hours, and use high-speed centrifugation to separate solid and liquid after cooling to obtain a solution containing zinc.
[0037] The leaching solution was fixed to a volume of 250 milliliters, and the concentration of zinc in it was detected after acidification and dilution, and it was calculated that after the zinc oxide raw ore was calcined at 600°C, the zinc leaching rate of alkali leaching was 87.33%.
[0038] Judging from the results of the examples and comparative tests, the effect after finely grinding and calcining the ore of zinc oxide is obviously better than that without calcining, and the leaching rate of zinc by alkali leaching is 7%-12% higher.
PUM
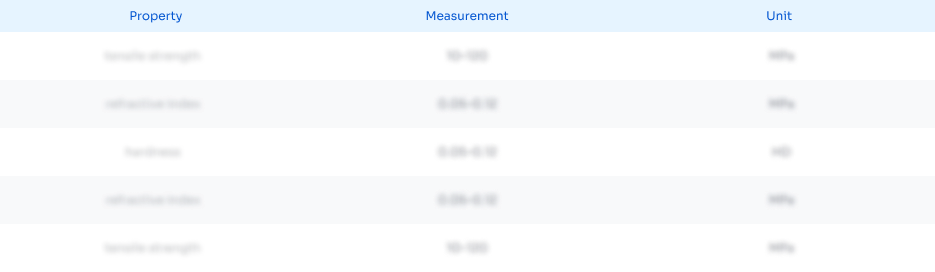
Abstract
Description
Claims
Application Information

- R&D
- Intellectual Property
- Life Sciences
- Materials
- Tech Scout
- Unparalleled Data Quality
- Higher Quality Content
- 60% Fewer Hallucinations
Browse by: Latest US Patents, China's latest patents, Technical Efficacy Thesaurus, Application Domain, Technology Topic, Popular Technical Reports.
© 2025 PatSnap. All rights reserved.Legal|Privacy policy|Modern Slavery Act Transparency Statement|Sitemap|About US| Contact US: help@patsnap.com