PC/ABS alloy and preparation method thereof
A technology of alloy and flame retardant synergist, which is applied in the field of PC/ABS alloy and its preparation, can solve the problems of limited development of halogen-based flame retardants, large amount of smoke, toxic gases, etc., and achieve excellent matt effect, resistance to The effect of good flammability and excellent processing performance
- Summary
- Abstract
- Description
- Claims
- Application Information
AI Technical Summary
Problems solved by technology
Method used
Image
Examples
Embodiment 1
[0054] Add 10% of halogen-free flame retardant, 1% of flame retardant and anti-dripping agent, 5% of toughening agent, 1% of compatibilizer, 1% of low gloss treatment agent, and 1% of antioxidant into the high-speed batch mixer, and then Drop 3% of the melted halogen-free flame retardant synergist into the blender and stir for 5 minutes, and all the above components are in mass percentage. Then add the baked 60% PC and 18% ABS, and then stir together for 5 minutes for later use. Put the stirred mixture in a twin-screw machine to melt, extrude and granulate. The process conditions are as follows: twin-screw first stage temperature 220-230°C, second-stage temperature 230-240°C, third-stage temperature 240-250°C, mold temperature 60 ~100℃, residence time 1~2 minutes, pressure 10~15MPa.
[0055] In this embodiment, the toughening agent is a core-shell type ABS impact modifier with a rubber content of 60-80%. The compatibilizer is ABS grafted malanic anhydride with a graft rate o...
Embodiment 2
[0057] Example 2: Add 12% of halogen-free flame retardant, 0.1% of flame retardant and anti-dripping agent, 7.9% of toughening agent, 1% of compatibilizer, 2% of low gloss treatment agent, and 2% of antioxidant into high-speed batching In the blender, then drop 1% of the melted halogen-free flame retardant synergist into the blender, and stir for 5 minutes, and each of the above components is in mass percentage. Then add baked 62% PC and 12% ABS, then stir together for 7 minutes, and set aside. Put the stirred mixture in a twin-screw machine to melt, extrude and granulate. The process conditions are as follows: twin-screw first stage temperature 220-230°C, second-stage temperature 230-240°C, third-stage temperature 240-250°C, mold temperature 60 ~100℃, residence time 1~2 minutes, pressure 10~15MPa.
[0058] In this embodiment, the toughening agent is a core-shell type ABS impact modifier with a rubber content of 60-80%. The compatibilizer is ABS grafted malanic anhydride wit...
Embodiment 3
[0060] Example 3: Add 7% of halogen-free flame retardant, 0.5% of flame retardant and anti-dripping agent, 3% of toughening agent, 3% of compatibilizer, 3% of low gloss treatment agent, and 1% of antioxidant into high-speed batching In the blender, then drop 3% of the melted halogen-free flame retardant synergist into the blender, and stir for 5 minutes, and each of the above components is in mass percentage. Then add baked 67% PC and 12% ABS, then stir together for 8 minutes, and set aside. Put the stirred mixture in a twin-screw machine to melt, extrude and granulate. The process conditions are as follows: twin-screw first stage temperature 220-230°C, second-stage temperature 230-240°C, third-stage temperature 240-250°C, mold temperature 60 ~100℃, residence time 1~2 minutes, pressure 10~15MPa.
[0061] In this embodiment, the toughening agent is a core-shell type ABS impact modifier with a rubber content of 60-80%. The compatibilizer is ABS grafted malanic anhydride with a...
PUM
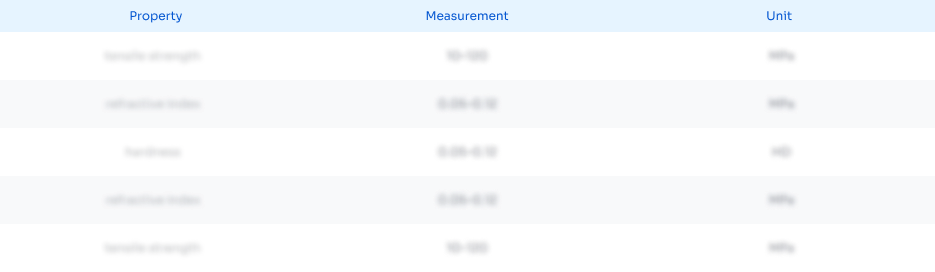
Abstract
Description
Claims
Application Information

- R&D
- Intellectual Property
- Life Sciences
- Materials
- Tech Scout
- Unparalleled Data Quality
- Higher Quality Content
- 60% Fewer Hallucinations
Browse by: Latest US Patents, China's latest patents, Technical Efficacy Thesaurus, Application Domain, Technology Topic, Popular Technical Reports.
© 2025 PatSnap. All rights reserved.Legal|Privacy policy|Modern Slavery Act Transparency Statement|Sitemap|About US| Contact US: help@patsnap.com