Preparation method of diamond particle reinforced copper-based composite material parts with high volume fraction
A technology of copper-based composite materials and diamond particles, which is applied in the field of metal materials, can solve the problems of high production cost and low production efficiency, and achieve the effects of simple production equipment, improved thermal conductivity, and improved holding force
- Summary
- Abstract
- Description
- Claims
- Application Information
AI Technical Summary
Problems solved by technology
Method used
Image
Examples
Embodiment 1
[0018] Example 1: Preparation of diamond-copper composite parts at 1450°C
[0019] Artificial diamond particles with an average particle size of 110 μm and titanium powder with an average particle size of 45 μm were mixed according to a volume ratio of 1:3, and mixed on a roller ball mill for 8 hours. Put the mixed powder of diamond and titanium into an alumina crucible and compact it, cover it with enough mixed salt of NaCl and KCl (the mass ratio of NaCl and KCl is 58:42), put it into a vacuum furnace and heat it to 850°C And keep it warm for 1 hour, take out the crucible and dissolve and separate the diamond particles.
[0020] Add 1-3% by mass and 10% polyvinyl alcohol (PVA) aqueous solution into the surface-modified diamond powder, mix well and fill the mixed powder into the mold cavity, press pressure The pressure is 6KN, and the holding time is 2 minutes, and the pressed body is placed in a drying oven to dry for 4 hours to obtain a diamond porous preform. Since the r...
Embodiment 2
[0022] Example 2: Preparation of diamond-copper alloy composite parts at 1350°C
[0023] Artificial diamond particles with an average particle size of 110 μm and titanium powder with an average particle size of 45 μm were mixed according to a volume ratio of 1:3, and mixed on a roller ball mill for 8 hours. Put the mixed powder of diamond and titanium into an alumina crucible and compact it, cover it with enough mixed salt of NaCl and KCl (the mass ratio of NaCl and KCl is 58:42), put it into a vacuum furnace and heat it to 850°C And keep it warm for 1 hour, take out the crucible and dissolve and separate the diamond particles.
[0024] Add 1-3% by mass and 10% polyvinyl alcohol (PVA) aqueous solution into the surface-modified diamond powder, mix well and fill the mixed powder into the mold cavity, press pressure The pressure is 6KN, and the holding time is 2 minutes, and the pressed body is placed in a drying oven to dry for 4 hours to obtain a diamond porous preform. Since...
Embodiment 3
[0026] Example 3: Preparation of diamond-copper alloy composite parts at 1400°C
[0027] Artificial diamond particles with an average particle size of 110 μm and titanium powder with an average particle size of 45 μm were mixed according to a volume ratio of 1:3, and mixed on a roller ball mill for 8 hours. Put the mixed powder of diamond and titanium into an alumina crucible and compact it, cover it with enough mixed salt of NaCl and KCl (the mass ratio of NaCl and KCl is 58:42), put it into a vacuum furnace and heat it to 850°C And keep it warm for 1 hour, take out the crucible and dissolve and separate the diamond particles.
[0028] Add 1-3% by mass and 10% polyvinyl alcohol (PVA) aqueous solution into the surface-modified diamond powder, mix well and fill the mixed powder into the mold cavity, press pressure The pressure is 6KN, and the holding time is 2 minutes, and the pressed body is placed in a drying oven to dry for 4 hours to obtain a diamond porous preform. Since...
PUM
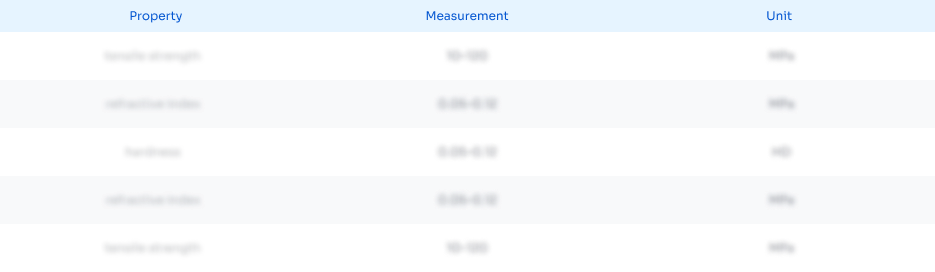
Abstract
Description
Claims
Application Information

- R&D
- Intellectual Property
- Life Sciences
- Materials
- Tech Scout
- Unparalleled Data Quality
- Higher Quality Content
- 60% Fewer Hallucinations
Browse by: Latest US Patents, China's latest patents, Technical Efficacy Thesaurus, Application Domain, Technology Topic, Popular Technical Reports.
© 2025 PatSnap. All rights reserved.Legal|Privacy policy|Modern Slavery Act Transparency Statement|Sitemap|About US| Contact US: help@patsnap.com