Method for sealing stainless steel and ceramic
A technology of stainless steel and ceramics, applied in the field of metallurgy, can solve the problems of high price and high product cost
- Summary
- Abstract
- Description
- Claims
- Application Information
AI Technical Summary
Problems solved by technology
Method used
Image
Examples
Embodiment 1
[0018] a. Immerse the stainless steel parts in sodium hydroxide (NaOH) with a concentration of 50g / L and a temperature of 60°C for 4 hours. After taking it out, wash it thoroughly in warm water, then wash it with cold water, dehydrate it with absolute ethanol, dry it, and remove it. grease, dirt;
[0019] b. the stainless steel parts 1 and 3 obtained in step a are used as anodes, and the cathode is made of lead. The electrolyte formula and polishing specifications are: orthophosphoric acid (H3PO4) 65%, sulfuric acid (H2SO4) 15%, chromic anhydride (CrO3) 6% , 14% deionized water, current density 0.2A / cm 2 , voltage 12V, working temperature 75°C, time 5min; after electropolishing, put the parts in 5% ammonia water and neutralize them for 20s, then wash them with water, dehydrate them with absolute ethanol, and dry them to remove the surface scale;
[0020] c. Nickel-plate the stainless steel parts 1 and 3 obtained in step b, and burn them in a hydrogen furnace to 800° C., keep ...
Embodiment 2
[0024] a. Immerse the stainless steel parts in sodium hydroxide (NaOH) with a concentration of 100g / L and a temperature of 60°C for 2 hours. After taking it out, wash it thoroughly in warm water, then wash it with cold water, dehydrate it with absolute ethanol, dry it, and remove it. grease, dirt;
[0025] b. the stainless steel parts 1 and 3 obtained in step a are used as anodes, and the cathode is made of lead. The electrolyte formula and polishing specifications are: orthophosphoric acid (H3PO4) 65%, sulfuric acid (H2SO4) 15%, chromic anhydride (CrO3) 6% , 14% deionized water, current density 0.5A / cm 2 , voltage 6V, working temperature 75°C, time 10min; after electropolishing, put the parts into 5% ammonia water to neutralize for 15s, then wash with water, dehydrate with absolute ethanol, and dry to remove the surface scale;
[0026] c. Nickel-plate the stainless steel parts 1 and 3 obtained in step b, and burn them in a hydrogen furnace to 800° C., keep the heat for 20 mi...
Embodiment 3
[0030] a. Immerse the stainless steel parts in sodium hydroxide (NaOH) with a concentration of 75g / L and a temperature of 60°C for 3 hours. After taking it out, wash it thoroughly in warm water, then wash it with cold water, dehydrate it with absolute ethanol, dry it, and remove it. grease, dirt;
[0031] b. the stainless steel parts 1 and 3 obtained in step a are used as anodes, and the cathode is made of lead. The electrolyte formula and polishing specifications are: orthophosphoric acid (H3PO4) 65%, sulfuric acid (H2SO4) 15%, chromic anhydride (CrO3) 6% , 14% deionized water, current density 0.4A / cm 2 , voltage 8V, working temperature 75°C, time 8min; after electropolishing, put the parts into 4% ammonia water to neutralize for 13s, then wash with water, dehydrate with absolute ethanol, and dry to remove the surface scale;
[0032] c. Nickel-plate the stainless steel parts 1 and 3 obtained in step b, and burn them in a vacuum furnace to 800°C, keep them warm for 20 minutes...
PUM
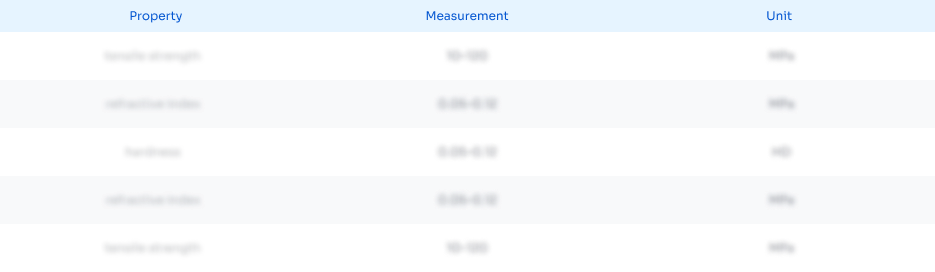
Abstract
Description
Claims
Application Information

- R&D Engineer
- R&D Manager
- IP Professional
- Industry Leading Data Capabilities
- Powerful AI technology
- Patent DNA Extraction
Browse by: Latest US Patents, China's latest patents, Technical Efficacy Thesaurus, Application Domain, Technology Topic, Popular Technical Reports.
© 2024 PatSnap. All rights reserved.Legal|Privacy policy|Modern Slavery Act Transparency Statement|Sitemap|About US| Contact US: help@patsnap.com