Low hardness high-performance glass mold and cast-iron flame-spray welding nickel base alloy powder
A glass mold, nickel-based alloy technology, applied in fusion spraying, metal material coating process, coating and other directions, can solve the problems of poor self-fluxing, welding layer temperature resistance, corrosion resistance and wear resistance, product defects and other problems , to achieve the effect of size out-of-tolerance repair, strong temperature resistance, and excellent processing performance
- Summary
- Abstract
- Description
- Claims
- Application Information
AI Technical Summary
Problems solved by technology
Method used
Examples
Embodiment Construction
[0006] The nickel-based alloy powder of the present invention is calculated by weight %, consisting of C: 0.01% to 0.2%, P: 1.0% to 3.0%, Cr: 1.5% to 6.0%, Si: 1.0% to 3.0%, and B: 0.1% to 1.2% % and Ni: The balance is composed of alloy powder made by atomization method. Apply the powder flame spray welding process to spray and weld it to the surface of castings such as glass molds and cast iron, because Ni in it can provide a good solid solution matrix, and B compounds are distributed on the Ni-Cr solid solution, and the B compounds are mainly It is composed of B, C and Cr, which makes the welding layer of the workpiece to be sprayed and welded wear-resistant; due to the addition of B and Si, it plays the role of fluxing and slagging, thereby improving its self-fluxing property; the addition of P , and lower the melting point of the nickel-based alloy powder, while enhancing the corrosion resistance of the welding layer of the workpiece to be sprayed. By controlling the comp...
PUM
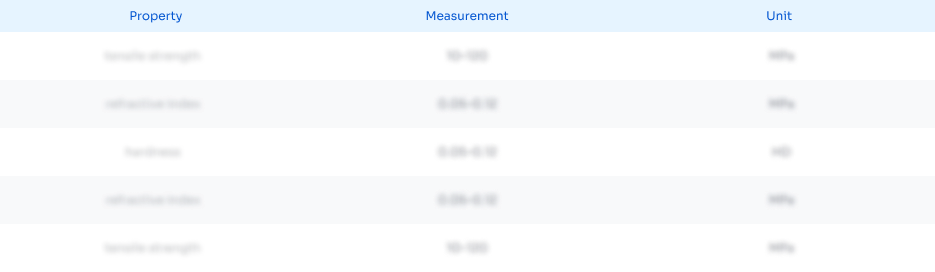
Abstract
Description
Claims
Application Information

- R&D
- Intellectual Property
- Life Sciences
- Materials
- Tech Scout
- Unparalleled Data Quality
- Higher Quality Content
- 60% Fewer Hallucinations
Browse by: Latest US Patents, China's latest patents, Technical Efficacy Thesaurus, Application Domain, Technology Topic, Popular Technical Reports.
© 2025 PatSnap. All rights reserved.Legal|Privacy policy|Modern Slavery Act Transparency Statement|Sitemap|About US| Contact US: help@patsnap.com