Integral type metal carrier three-way catalyst and preparation method thereof
A three-way catalyst and metal carrier technology, applied in metal/metal oxide/metal hydroxide catalysts, chemical instruments and methods, physical/chemical process catalysts, etc., can solve the problems of large power consumption and time, cracking, production Cost prolongation of production cycle and other issues
- Summary
- Abstract
- Description
- Claims
- Application Information
AI Technical Summary
Problems solved by technology
Method used
Examples
example 1
[0026] Take by weighing 100g of active alumina pulverized by jet mill, 30g of cerium-zirconium solid solution, 10g of cerium nitrate, 5g of lanthanum nitrate, 2g of magnesium nitrate, 4g of palladium nitrate, 1g of rhodium nitrate, add 360ml deionized water, under mechanical stirring, add concentrated Adjust the pH to 4 with nitric acid, control the viscosity at 600mPa·S, and stir for 20 minutes. The metal carrier is placed in a vacuum environment, the prepared composite slurry is vacuum sprayed on the carrier, and after keeping for 5-15 minutes, the excess slurry in the channels is removed by vacuum extraction. The coated carrier was dried at 120° C. for 12 hours, and then calcined at 600° C. for 2 hours, and the preparation of the catalyst was completed. The loading rate of one coating is shown in the table below:
[0027]
Mass of metal carrier before coating / g
Mass of metal carrier after coating / g
load factor
1
8.873
9.682
9.27%...
example 2
[0031] Take by weighing 100g of active alumina pulverized by jet mill, 30g of cerium-zirconium solid solution, 10g of cerium nitrate, 5g of lanthanum nitrate, 2g of barium nitrate, 4.5g of palladium nitrate, 1.5g of rhodium nitrate, 1.5g of platinum nitrate, add 220ml of deionized water, Under mechanical stirring, add concentrated nitric acid to adjust the pH to 2.5, control the viscosity at 4500mPa·S, and stir for 20 minutes. The metal carrier is placed in a vacuum environment, the prepared composite slurry is vacuum sprayed on the carrier, and after keeping for 5-15 minutes, the excess slurry in the channels is removed by vacuum extraction. The coated carrier was dried at 120° C. for 12 hours, and then calcined at 600° C. for 2 hours, and the preparation of the catalyst was completed. The loading rate of one coating is shown in the table below:
[0032]
Mass of metal carrier before coating / g
Mass of metal carrier after coating / g
load factor
1
...
PUM
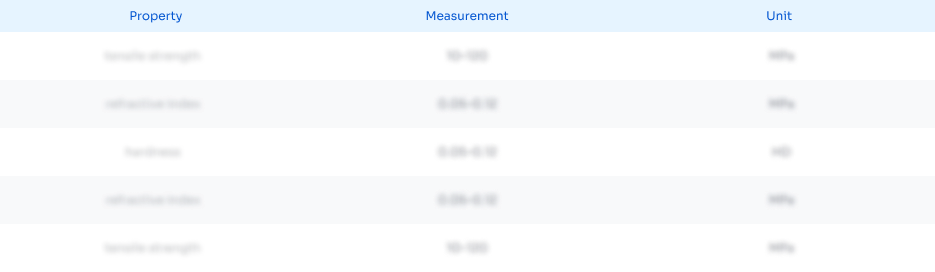
Abstract
Description
Claims
Application Information

- R&D Engineer
- R&D Manager
- IP Professional
- Industry Leading Data Capabilities
- Powerful AI technology
- Patent DNA Extraction
Browse by: Latest US Patents, China's latest patents, Technical Efficacy Thesaurus, Application Domain, Technology Topic, Popular Technical Reports.
© 2024 PatSnap. All rights reserved.Legal|Privacy policy|Modern Slavery Act Transparency Statement|Sitemap|About US| Contact US: help@patsnap.com