Method for increasing nitrogen content of vanadium-nitrogen alloy
A vanadium-nitrogen alloy and nitrogen content technology, which is applied in the field of vanadium-containing oxide smelting, can solve the problems of large fluctuation range of nitrogen content, small scale output and high cost, and achieves low preparation cost and energy consumption, simple production and high price. low cost effect
- Summary
- Abstract
- Description
- Claims
- Application Information
AI Technical Summary
Problems solved by technology
Method used
Examples
Embodiment 1
[0037] Grind 1000kg of vanadium tetroxide and vanadium pentoxide powder with a vanadium content of 60% finely to -100 mesh, add 300kg of graphite, 5kg of iron powder, 5kg of polyvinyl alcohol, 5kg of ferrous carbonate, and dry mix 25 minutes until uniform, add appropriate amount of water and wet mix for 25 minutes until uniform; apply a pressure of 9MPa to the wet-mixed mixture and press it into a 50 mm × 50 mm × 30 mm wet block, and the wet block is at 200 ° C. Heating and drying for 50 hours to obtain a dry block; the dry block is carbonized at atmospheric pressure and high temperature and calcined in a nitriding furnace. The calcination temperature is 1550°C, and the calcination time is 28 hours. The sintered block is cooled to below 100°C with the furnace After being released from the furnace, a vanadium-nitrogen alloy product with a nitrogen content of 17.50% was obtained.
[0038] In this embodiment, because the nitriding accelerator is added, the output of the vanadium-...
Embodiment 2
[0040] Finely grind 1000kg of a mixture of vanadium trioxide and vanadium tetroxide powder with a vanadium content of 61% to -100 mesh, add 290kg of carbon black, 6kg of iron powder, 7kg of flour, and 6kg of ammonium chloride, and dry mix for 25 minutes until uniform, add an appropriate amount of water and wet mix for 25 minutes until uniform; apply a pressure of 9 MPa to the wet-mixed mixture and press it into a wet material block of 50 mm × 50 mm × 30 mm, and heat the wet material block at 200 ° C. Dry for 50 hours to obtain a dry block; carbonize the dry block at high temperature under normal pressure and calcine in a nitriding furnace. The calcination temperature is 1550°C, and the calcination time is 28 hours. The sintered block is cooled to below 100°C with the furnace and released. A vanadium-nitrogen alloy product with a nitrogen content of 16.80% is obtained.
[0041] In this embodiment, because the nitriding accelerator is added, the output of the vanadium-nitrogen a...
Embodiment 3
[0043] Finely grind 1000kg of vanadium tetroxide powder with a vanadium content of 62% to -200 mesh, add 285kg of graphite, 7kg of iron powder, 9kg of polyvinyl alcohol, and 8kg of ammonium sulfate, dry mix for 25 minutes until uniform, and add an appropriate amount of water Wet mix for 25 minutes until uniform; apply a pressure of 9 MPa to the wet-mixed mixture and press it into a wet material block of 50 mm × 50 mm × 30 mm. The wet material block is heated at 200 ° C and dried for 50 hours to obtain a dry material block; carry out atmospheric pressure high temperature carbonization of the dry block and calcination in the nitriding furnace, the calcination temperature is 1550°C, the calcination time is 28 hours, the sintered block is cooled to below 100°C with the furnace, and the nitrogen content of % vanadium nitrogen alloy products.
[0044] In this embodiment, the output of vanadium-nitrogen alloy per 24 hours is 1570 kg due to the addition of the nitriding accelerator, w...
PUM
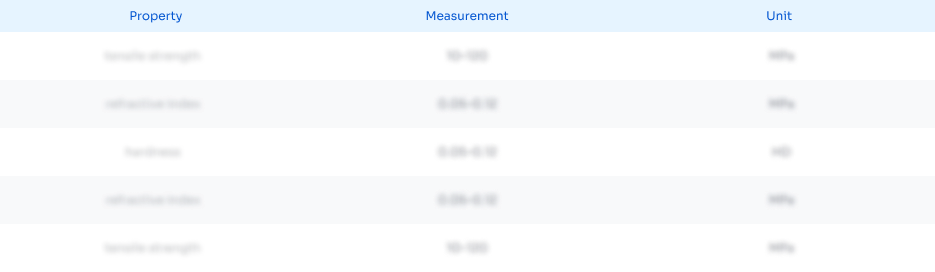
Abstract
Description
Claims
Application Information

- R&D
- Intellectual Property
- Life Sciences
- Materials
- Tech Scout
- Unparalleled Data Quality
- Higher Quality Content
- 60% Fewer Hallucinations
Browse by: Latest US Patents, China's latest patents, Technical Efficacy Thesaurus, Application Domain, Technology Topic, Popular Technical Reports.
© 2025 PatSnap. All rights reserved.Legal|Privacy policy|Modern Slavery Act Transparency Statement|Sitemap|About US| Contact US: help@patsnap.com