Method for simultaneously producing liquid fuel and asphalt paving materials by coprocessing coal and heavy oil
A liquid fuel and co-processing technology, which is applied in the processing of gas fuel, tar pitch/petroleum pitch/natural pitch, and fuel, etc., can solve the problems of inability to increase oil yield, reduce oil yield, etc., so as to reduce one-time investment and The effect of long-term operation cost, reduction of hydrogenation depth, and reduction of reaction severity
- Summary
- Abstract
- Description
- Claims
- Application Information
AI Technical Summary
Problems solved by technology
Method used
Image
Examples
Embodiment 1
[0044] Coal / catalytic cracking oil slurry=2 / 3 (wt, dry coal basis), red mud is used as a catalyst, and the addition amount is 3% (wt, dry coal basis). The above mixture is preheated to 310°C by a preheater, and reacted for 1 hour in a forced circulation ebullated bed reactor at 380-400°C and 10MPa hydrogen pressure.
[0045] The reaction product is separated by a high-temperature separator at 350°C and 10MPa, and the top product of the high-temperature separator enters a low-temperature separator at 200°C and 3MPa to separate into gas-liquid two-phase. The gaseous substances are purified by the eight-tower pressure swing adsorption device at 2.12MPa and 35°C. The separated hydrogen is returned to the reactor for recycling, and the rest of the gas is desulfurized and purified by the alcohol amine absorption method and used as fuel. The liquid product at the bottom of the low-temperature separator is condensed and separated from oil and water to obtain light oil. The bottom pro...
Embodiment 2
[0049] Coal / catalytic cracking oil slurry=1 / 1 (wt, based on dry coal), and molybdenum sulfide is added as a catalyst in an amount of 0.05% (wt, based on dry coal). The above mixture was preheated to 300° C. by a preheater, and reacted in a tubular reactor at 390° C. and 11 MPa hydrogen pressure for 1 hour.
[0050] The reaction product is separated by a high-temperature separator at 330°C and 11MPa. The top product of the separator is purified by an eight-column pressure swing adsorption device at 3.85MPa and 40°C. The separated hydrogen is returned to the reactor for recycling, and the rest The gas is used as fuel after desulfurization and purification by liquid phase redox method. Liquid and solid substances enter the flash tower with a temperature of 320°C and a pressure of 0.016 MPa, and the top product is condensed and separated from oil and water to obtain light oil. The bottom product is passed through the atmospheric distillation tower at 350°C and 0.138MPa operating ...
Embodiment 3
[0054] Coal / atmospheric residual oil=3 / 5 (wt, dry coal base), the preparation method of ultra-fine and highly dispersed iron-based catalysts is: add 7 g of saturated solution of ferrous sulfate to 100 g of coal sample, stir evenly, and then add 3.5 g Saturated solution of sodium sulfide, stirred evenly, and then vacuum-dried at 80°C for 5 hours to prepare an ultrafine and highly dispersed iron-based catalyst loaded on a coal sample. The addition amount of the superfine highly dispersed iron-based catalyst is 20% (wt, based on dry coal). The above mixture is preheated to 330° C. by a preheater, and reacted for 1.5 hours in a forced circulation suspended bed reactor at 400° C. and 8-10 MPa hydrogen pressure.
[0055] The reaction product is separated by a high-temperature separator at 360°C and 8-10MPa, and the top product of the high-temperature separator enters a low-temperature separator at 210°C and 3-4MPa to separate into gas-liquid two-phase. Gaseous substances are purifi...
PUM
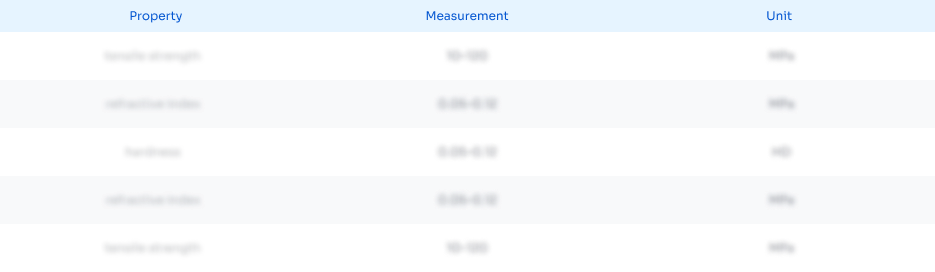
Abstract
Description
Claims
Application Information

- R&D
- Intellectual Property
- Life Sciences
- Materials
- Tech Scout
- Unparalleled Data Quality
- Higher Quality Content
- 60% Fewer Hallucinations
Browse by: Latest US Patents, China's latest patents, Technical Efficacy Thesaurus, Application Domain, Technology Topic, Popular Technical Reports.
© 2025 PatSnap. All rights reserved.Legal|Privacy policy|Modern Slavery Act Transparency Statement|Sitemap|About US| Contact US: help@patsnap.com