Liquid steel pre-deoxidizing technology in steelmaking revolving furnace
A steelmaking converter and pre-deoxidation technology, applied in the field of metallurgical steelmaking, can solve the problems of low service life of furnace lining ladle, poor quality of molten steel, and inability to reduce the FeO content of slag at the end of the converter
- Summary
- Abstract
- Description
- Claims
- Application Information
AI Technical Summary
Problems solved by technology
Method used
Examples
Embodiment Construction
[0015] The technical feature of the present invention is to carry out pre-deoxidation of molten steel in the steelmaking converter, which includes adding carbon-containing or silicon-containing deoxidizing materials to the slag liquid level in the converter through the high-level silo at the end of the smelting of the steelmaking converter, and using an oxygen lance or a converter The bottom blowing gun injects nitrogen into the converter as a power source, so that the carbon or silicon in the deoxidized material and the dissolved oxygen in molten steel are stirred and reacted at high temperature. The reaction process [C]+[O]={CO}, [ Si]+{O 2}=(SiO 2 ). The oxygen activity of molten steel is reduced by 96-757ppm, and the FeO content in the steel slag at the end of converter smelting is reduced by 1.3-10.6%. The carbon-containing deoxidizing material is coke powder or a coal-based recarburizer, and the amount of the carbon-containing deoxidizing material added is 1-4 kg per t...
PUM
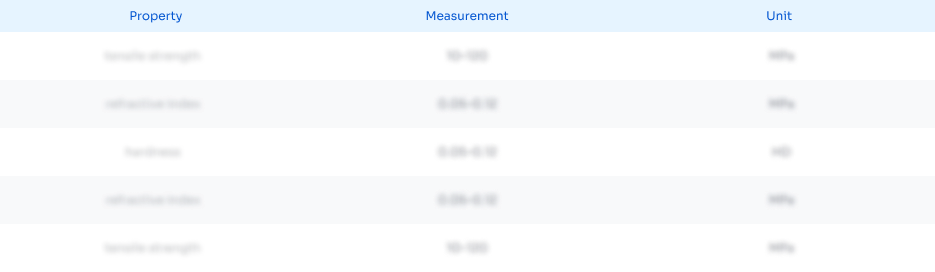
Abstract
Description
Claims
Application Information

- Generate Ideas
- Intellectual Property
- Life Sciences
- Materials
- Tech Scout
- Unparalleled Data Quality
- Higher Quality Content
- 60% Fewer Hallucinations
Browse by: Latest US Patents, China's latest patents, Technical Efficacy Thesaurus, Application Domain, Technology Topic, Popular Technical Reports.
© 2025 PatSnap. All rights reserved.Legal|Privacy policy|Modern Slavery Act Transparency Statement|Sitemap|About US| Contact US: help@patsnap.com